Case Studies
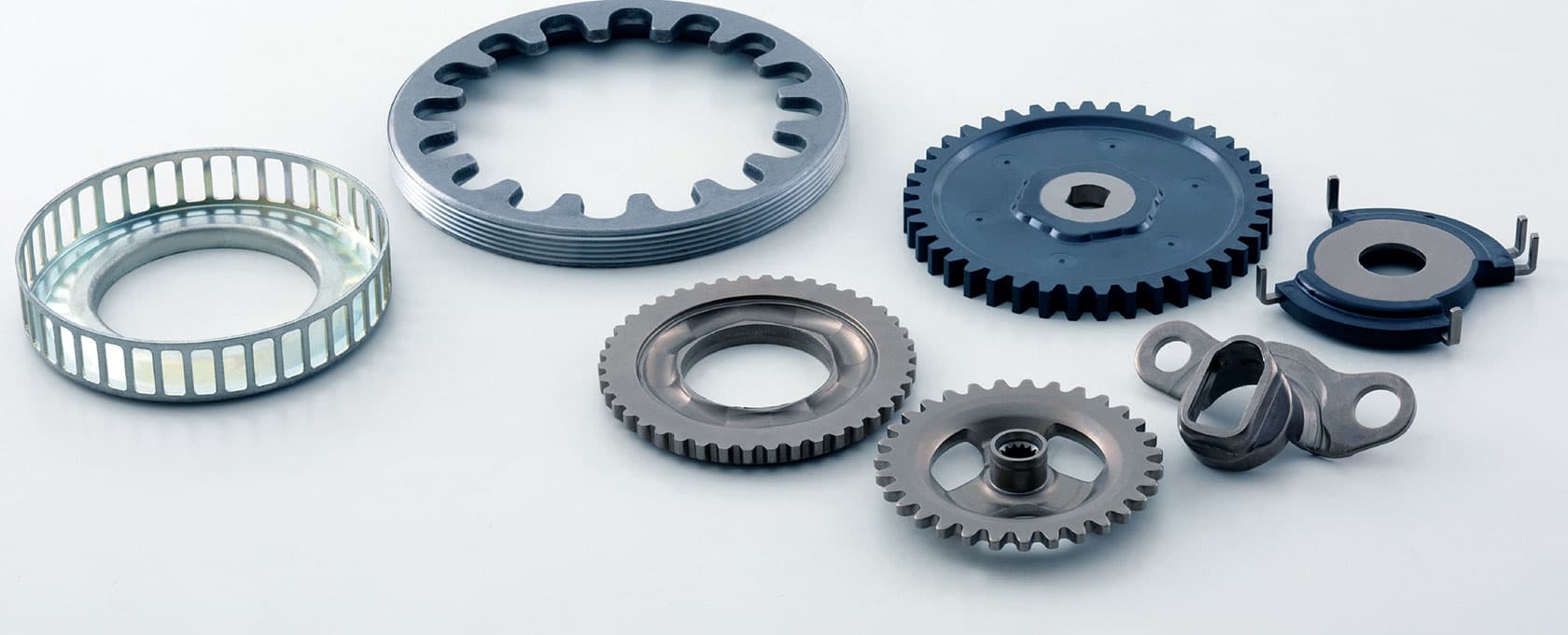
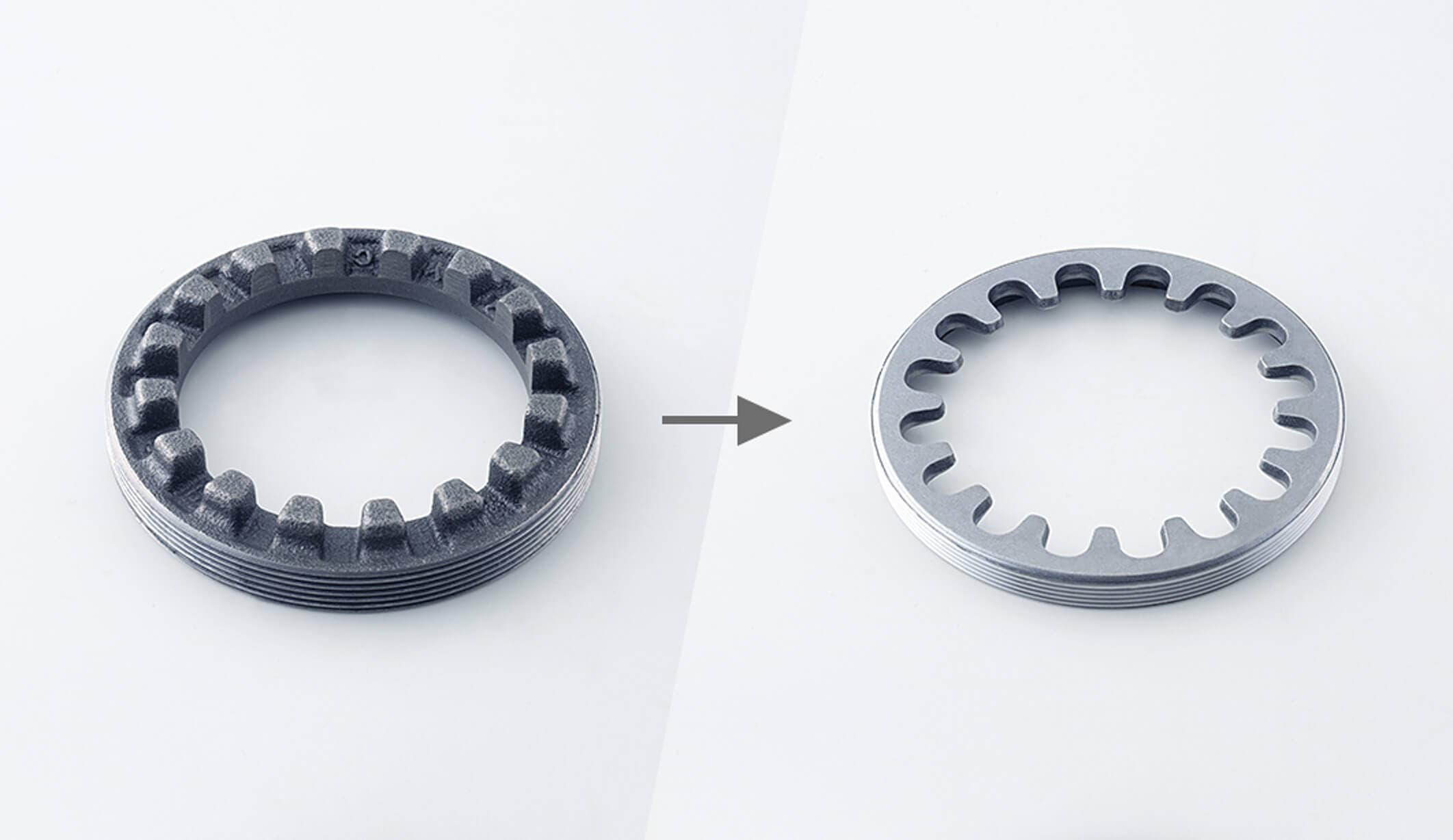
Case Summary
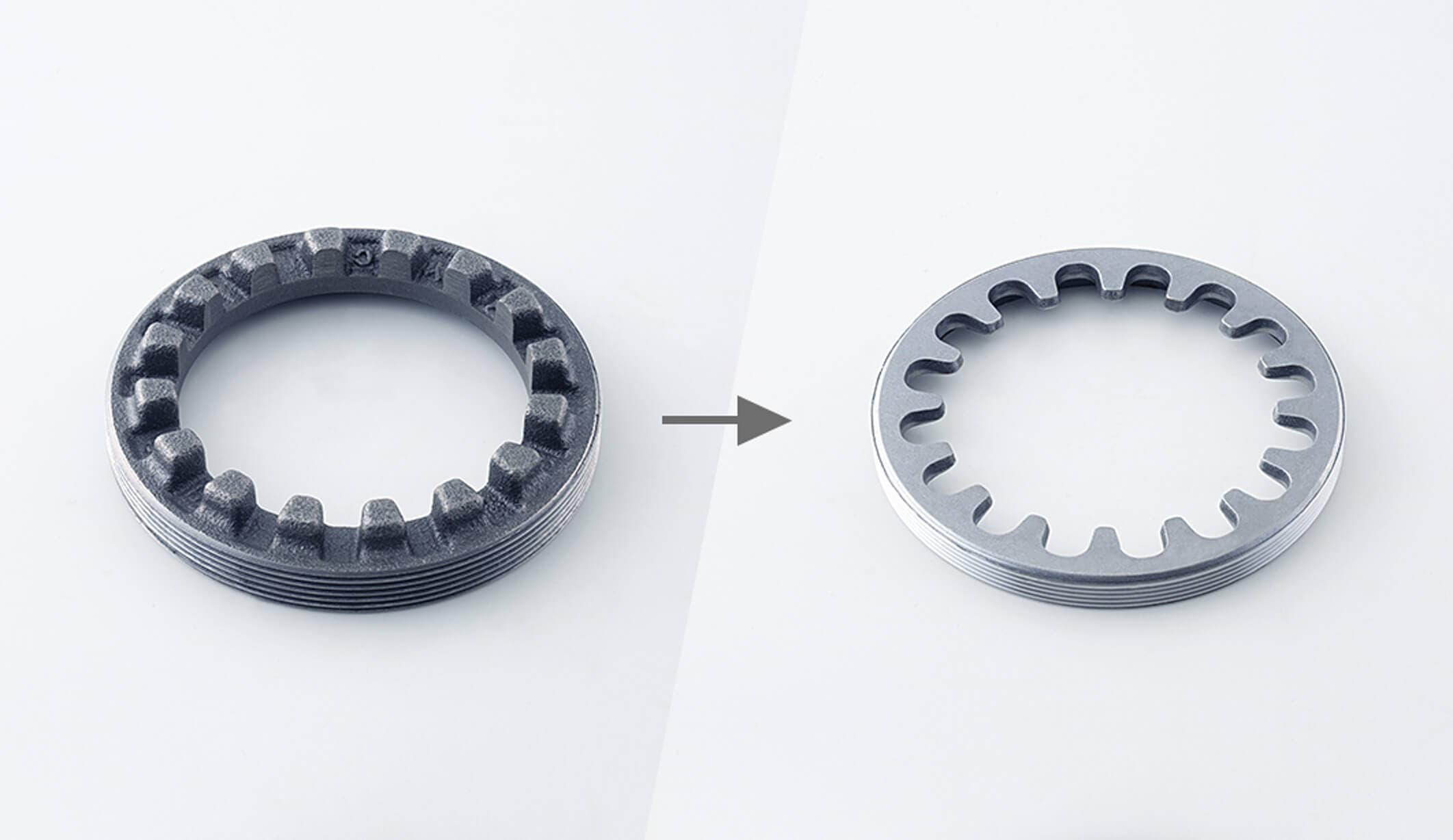
Converted from "sintering to thread cutting" to "pressing to thread cutting" method. Made a VE proposal that satisfied the functionality. We achieved approximately 15% price reduction and weight reduction compared to other companies conventional parts.
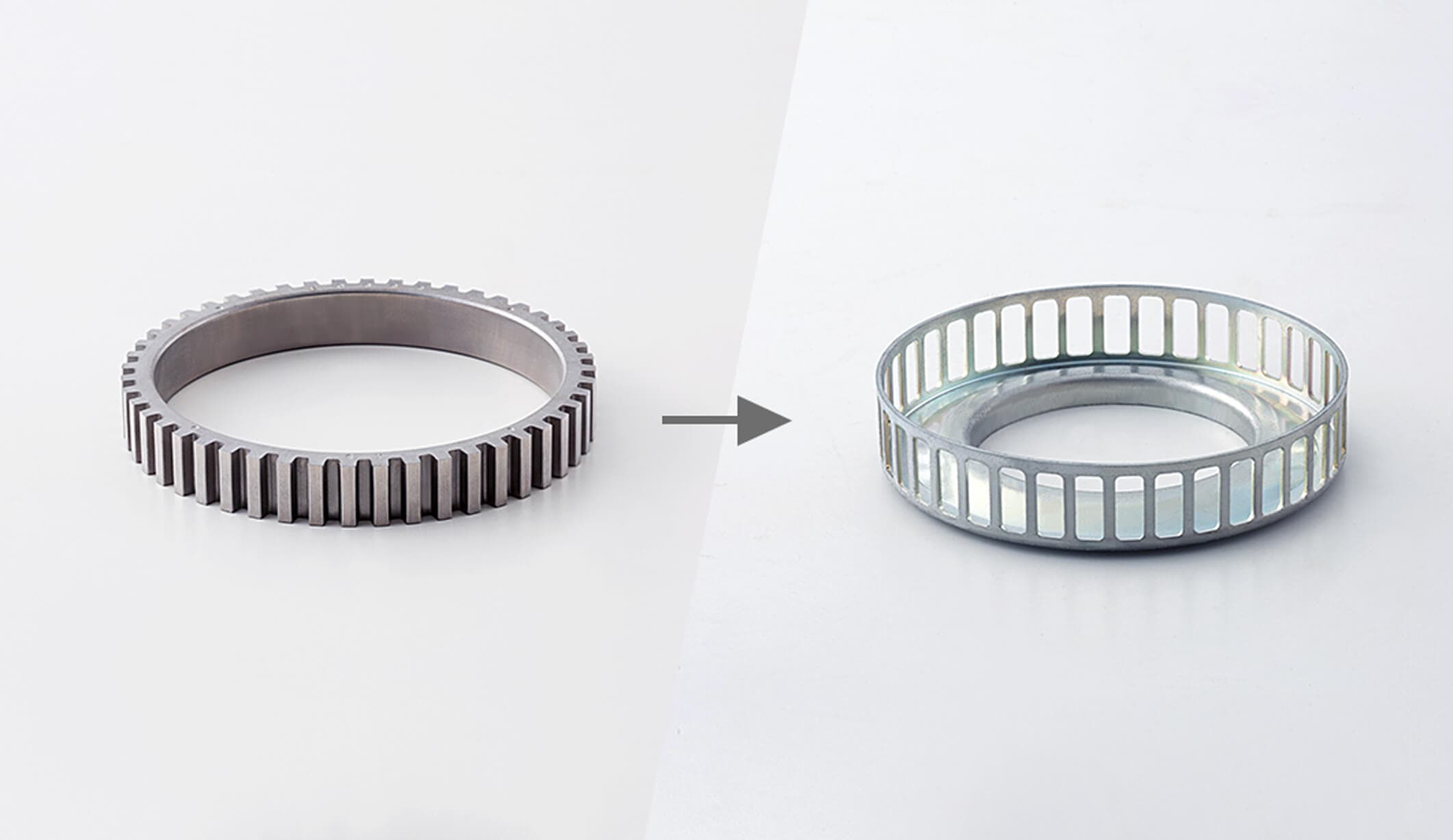
Case Summary
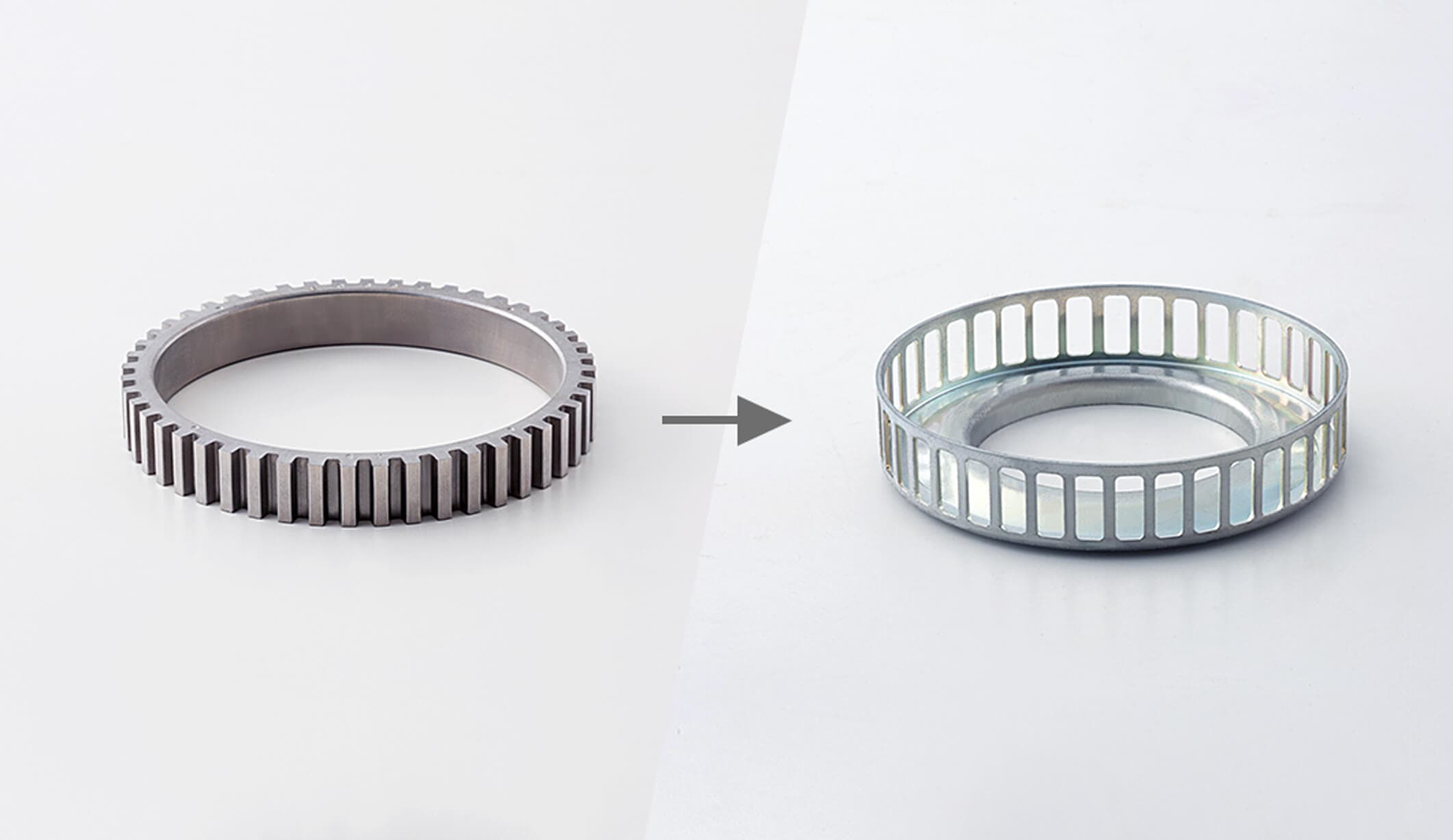
We proposed a window by press shape for the sensing part of the sintered speed sensor component of the differential. Furthermore, the required functions were satisfied with respect to the accuracy of the window and the press fitting accuracy of the inner diameter, resulting in 30% cost reduction.
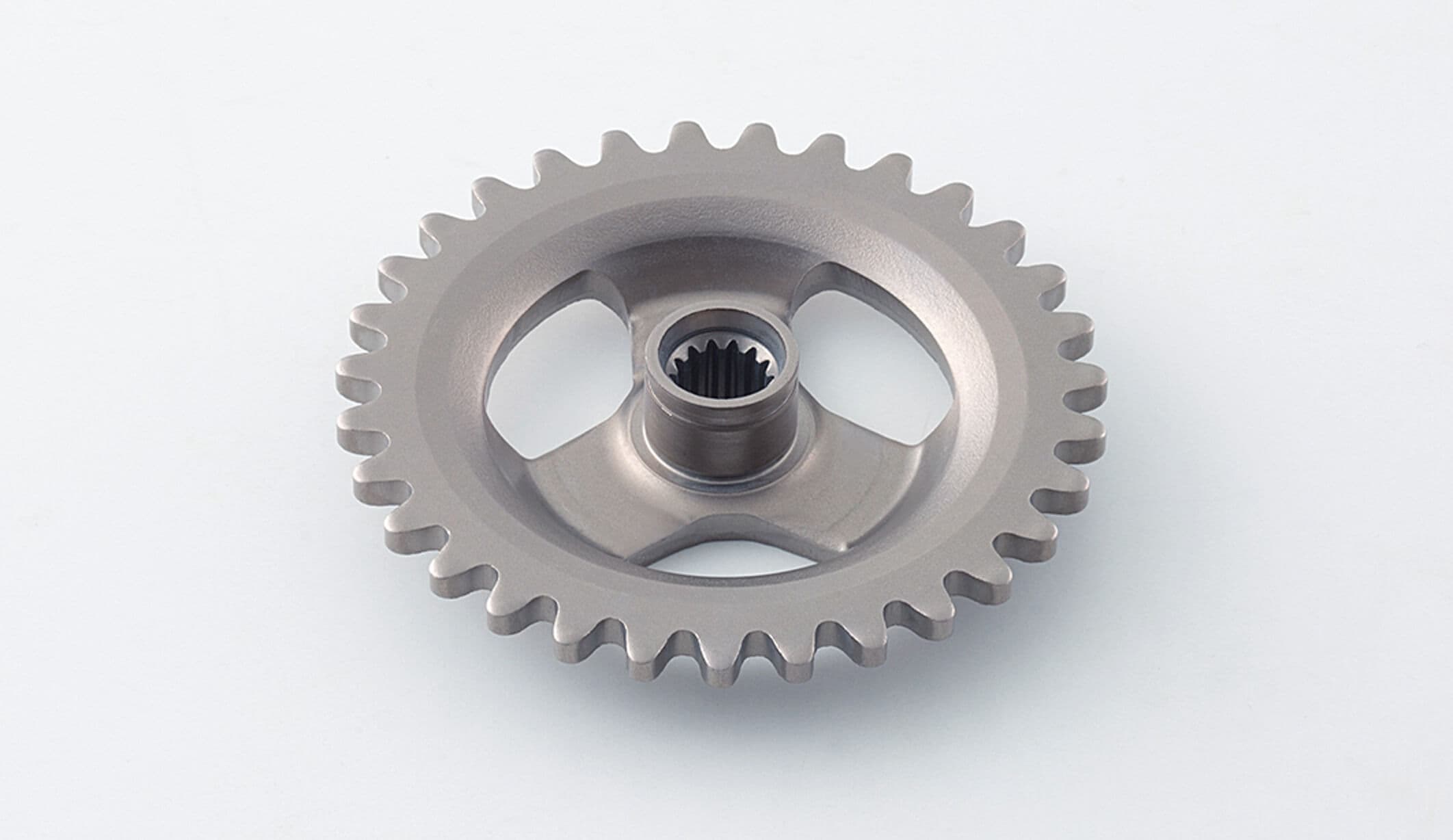
Case Summary
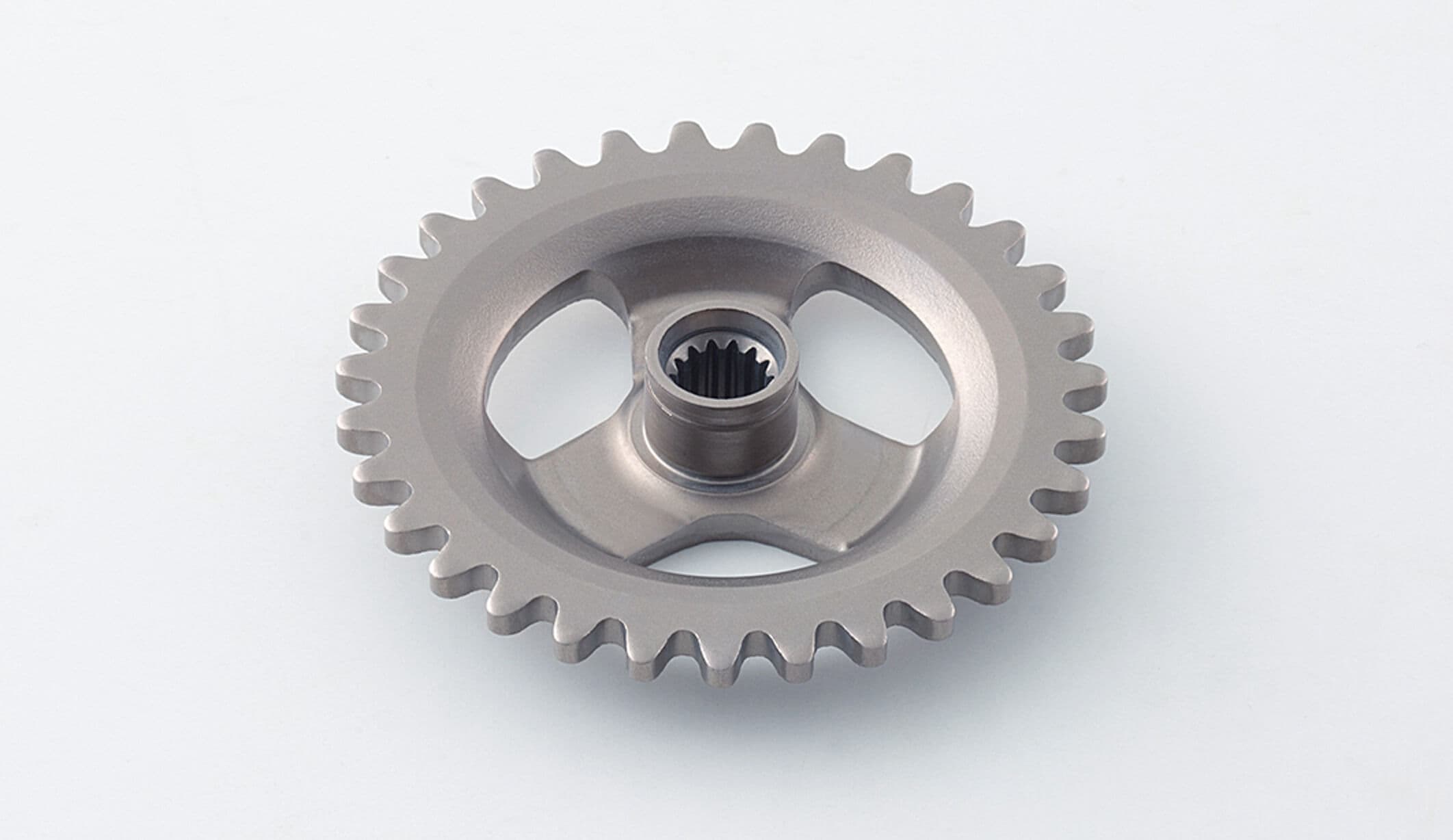
VE proposal for pressing instead of conventional broaching of the inner diameter part, resulting in 25% cost reduction and increased production capacity. Succeeded in pressing inner diameter part, which had been considered technically difficult.
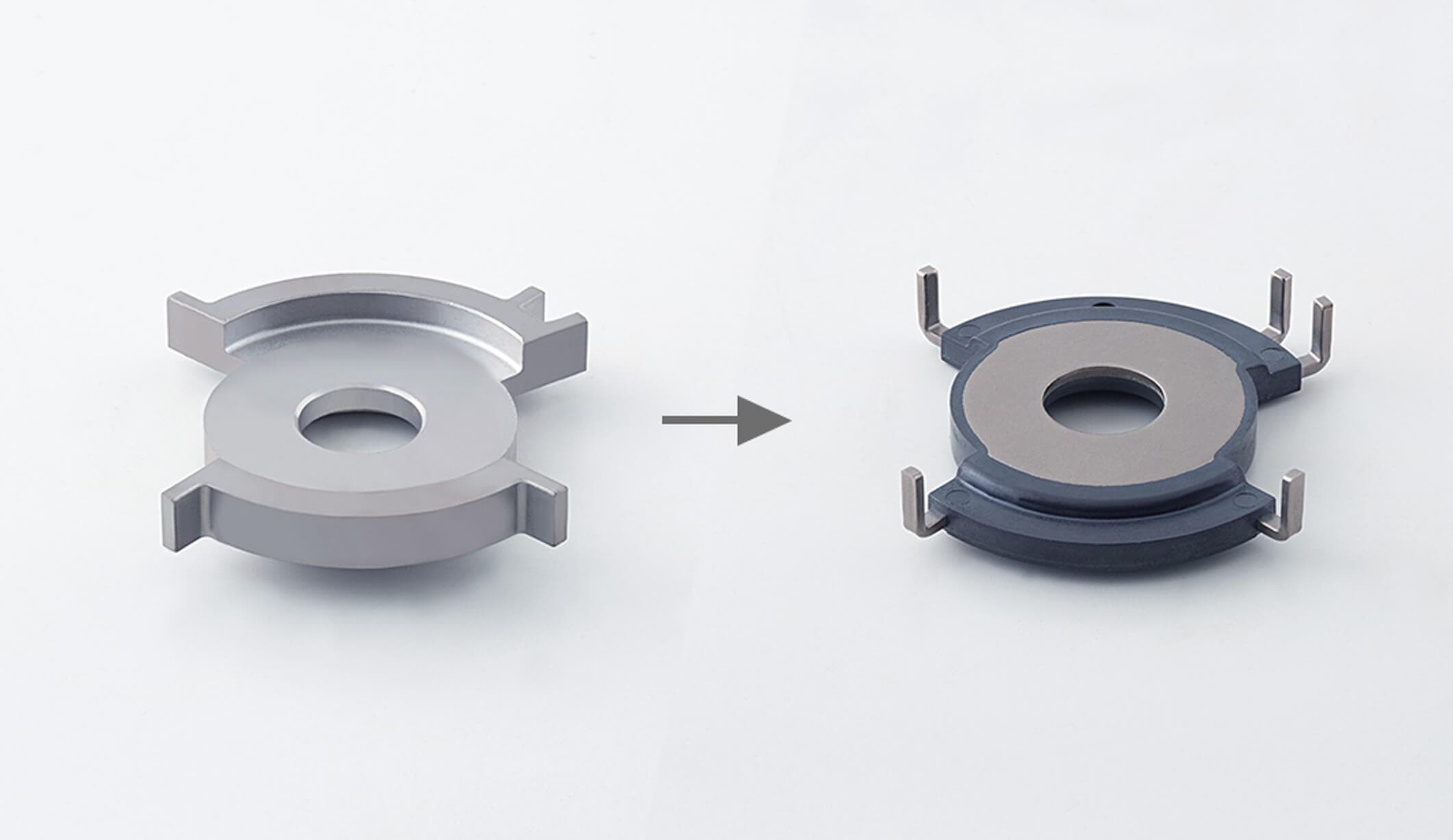
Case Summary
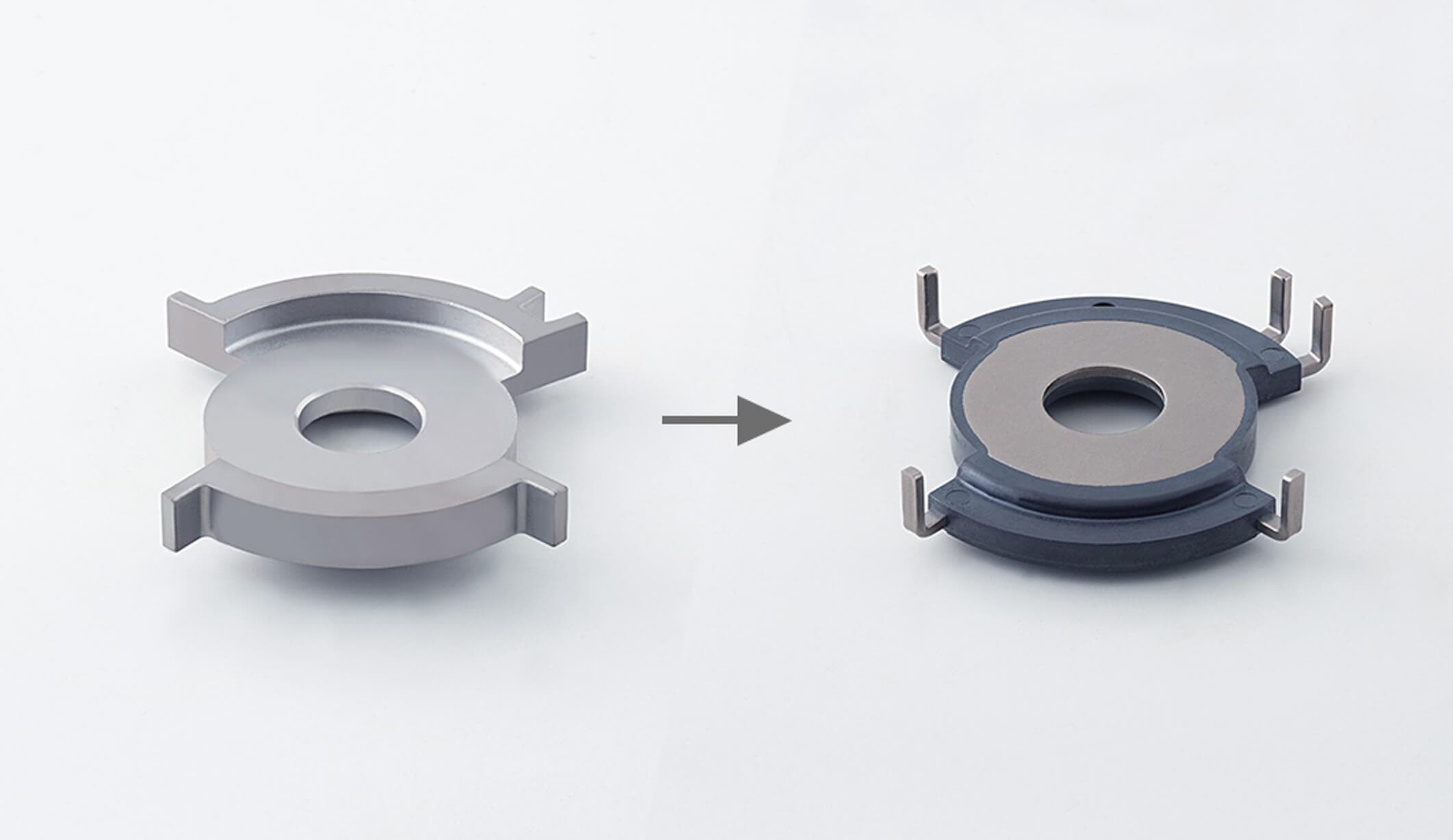
In order to secure the thickness of the molded product conventional sintering method, we made the necessary part with steel and the thick part with resin, resulting in strength and weight reduction.
Hybrid molded products utilizing the advantages of metal and resin.
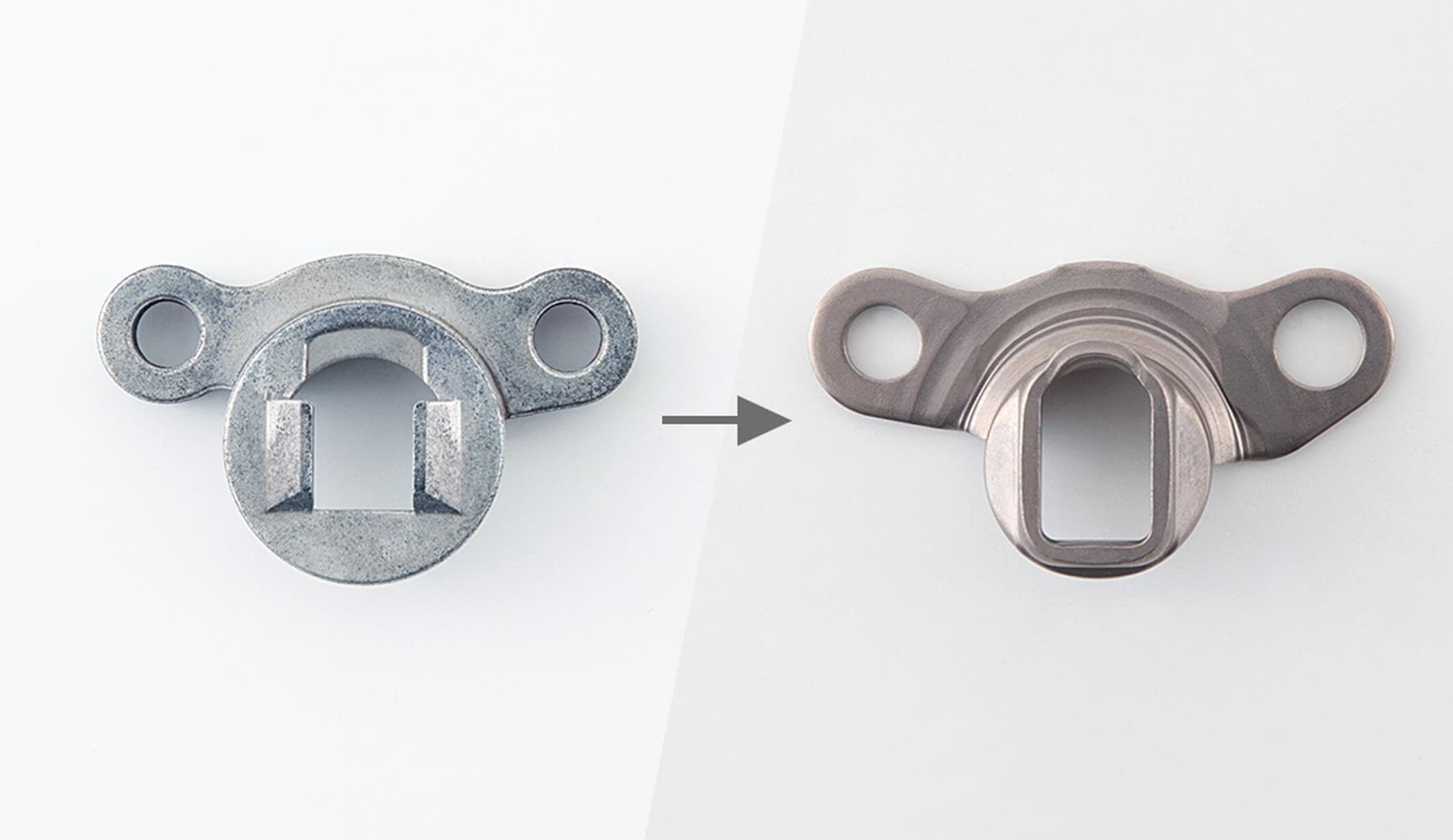
Case Summary
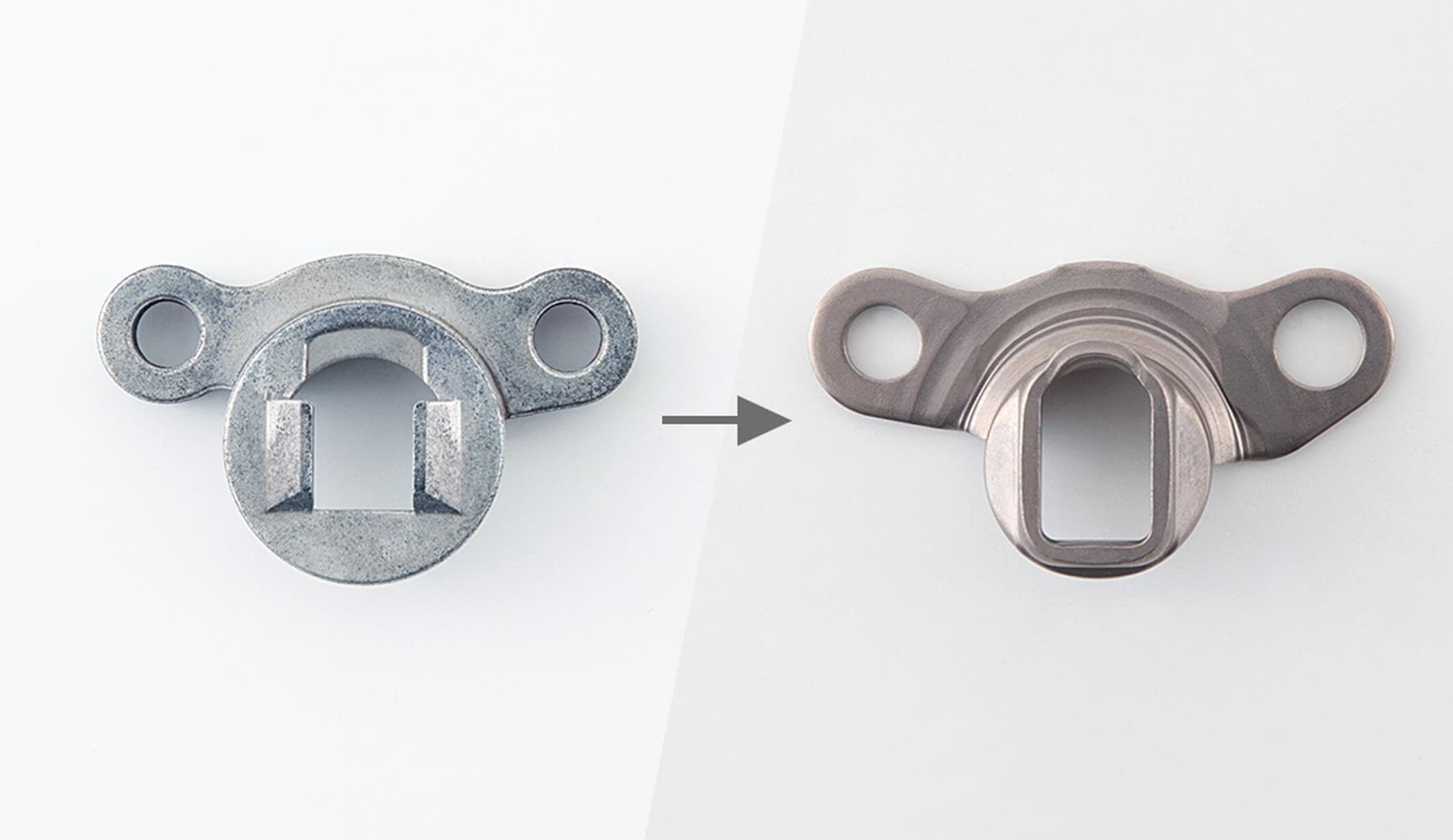
Cost reduction was achieved by converting the process from conventional sintering and machining to all-press processing.
Surface hardness was secured by carburizing and nitriding.
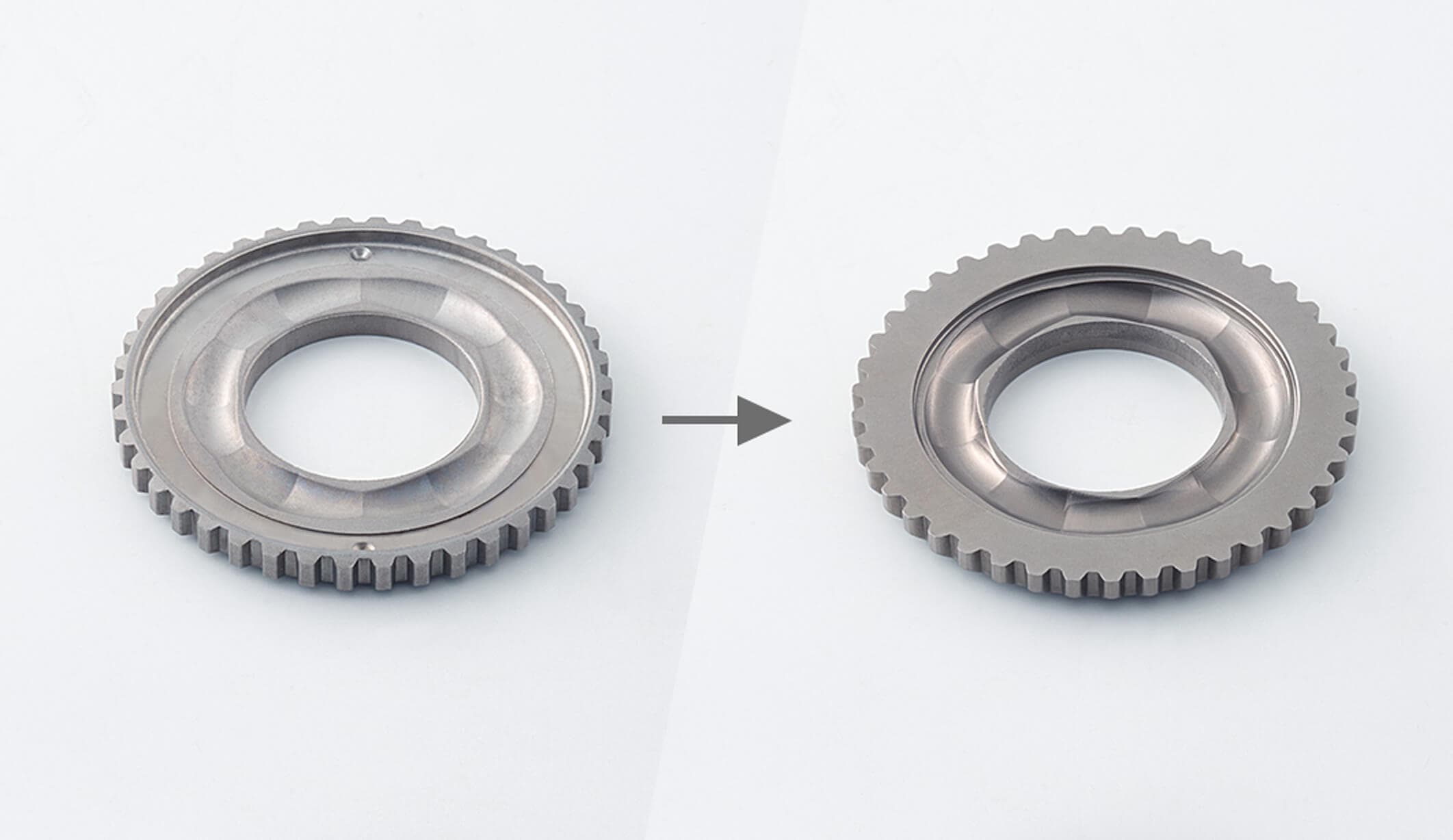
Case Summary
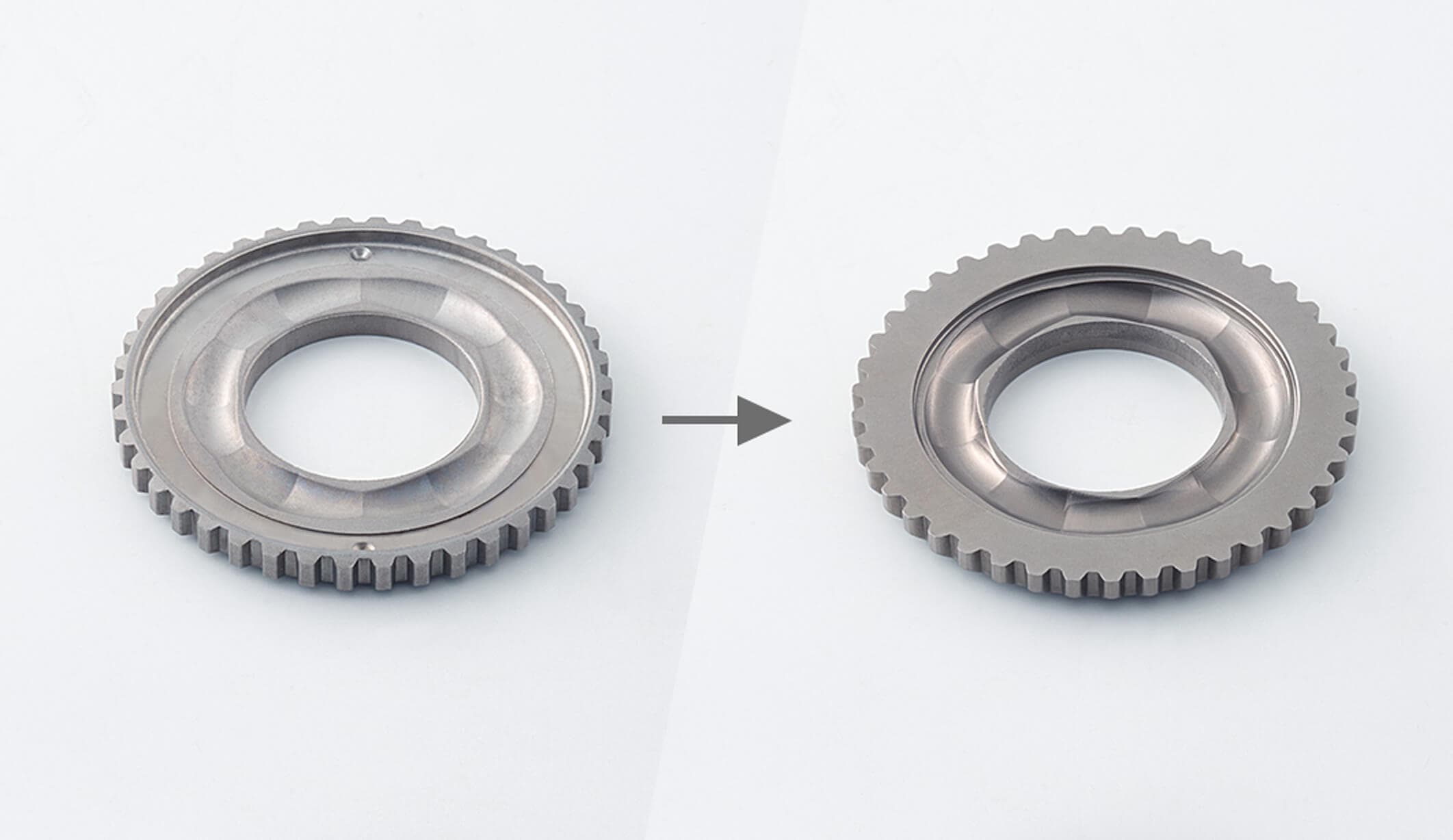
Cost reduction was achieved by converting the process from conventional sintering to pressing + cutting.
Surface hardness was secured by carburizing and nitriding.
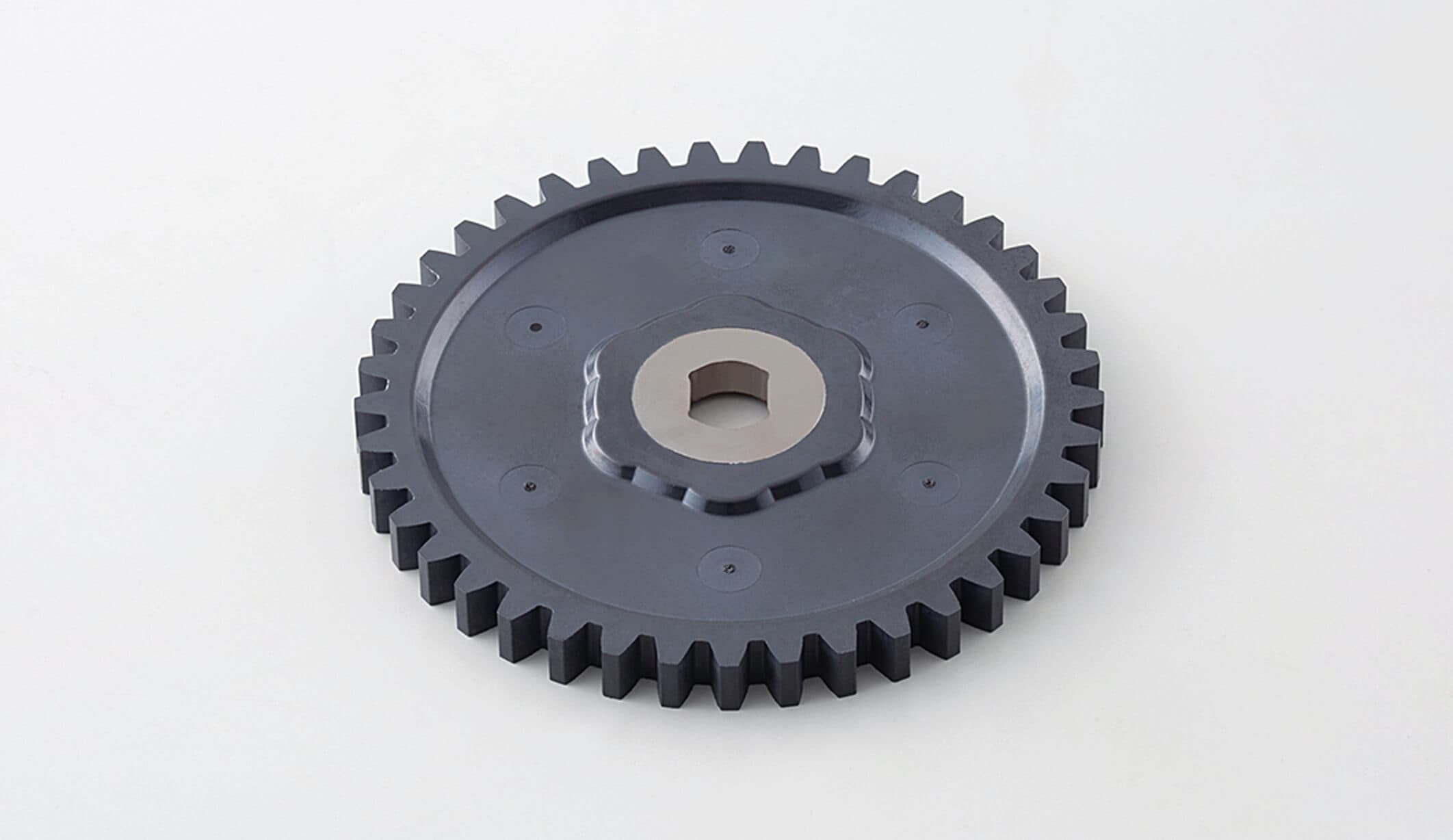
Case Summary
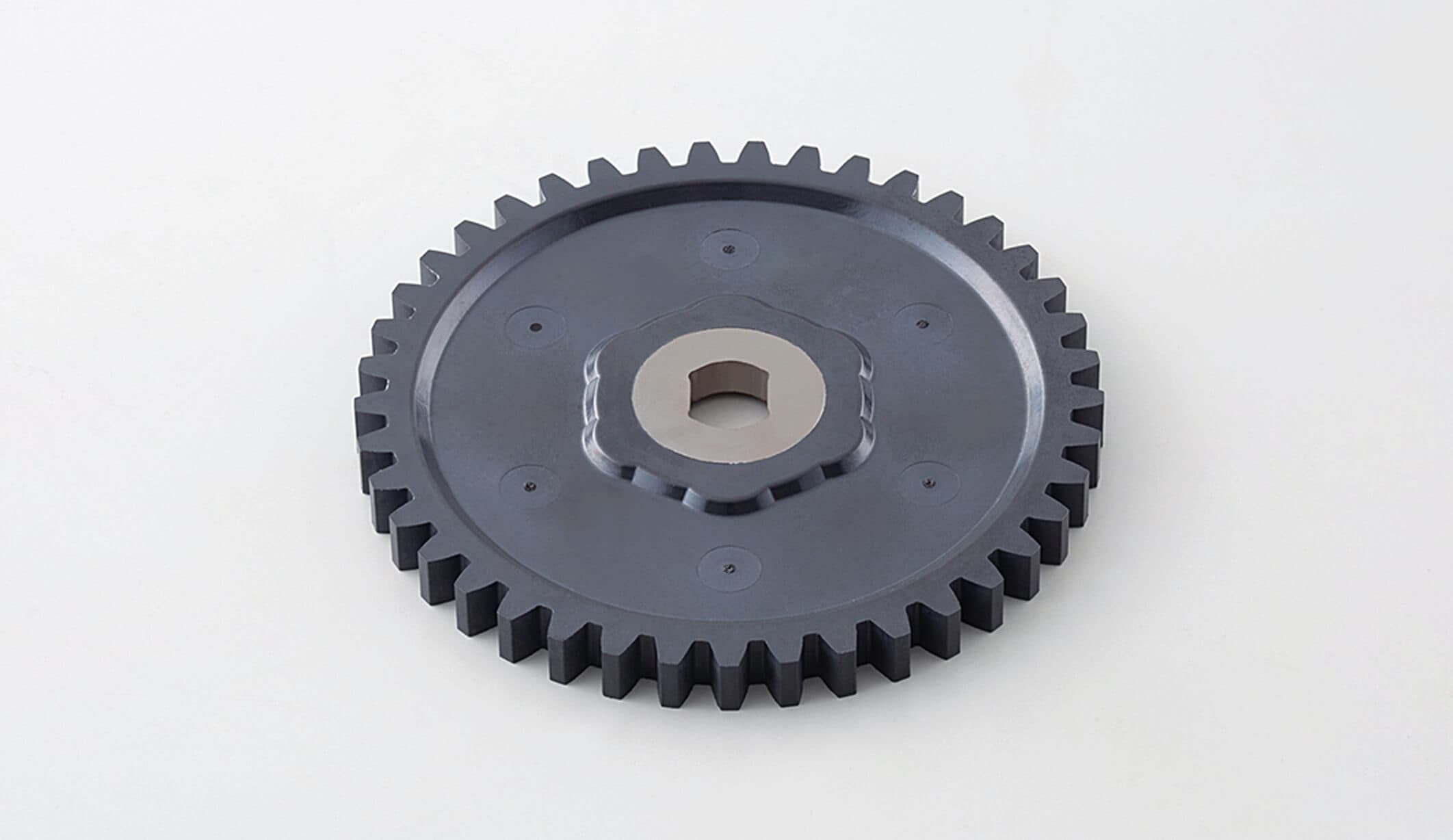
Forging + tooth cutting method" was successfully changed to press for fastening part and tooth part was changed to insert molding product.
Achieved strength enhancement and weight reduction.