Case Studies事例紹介
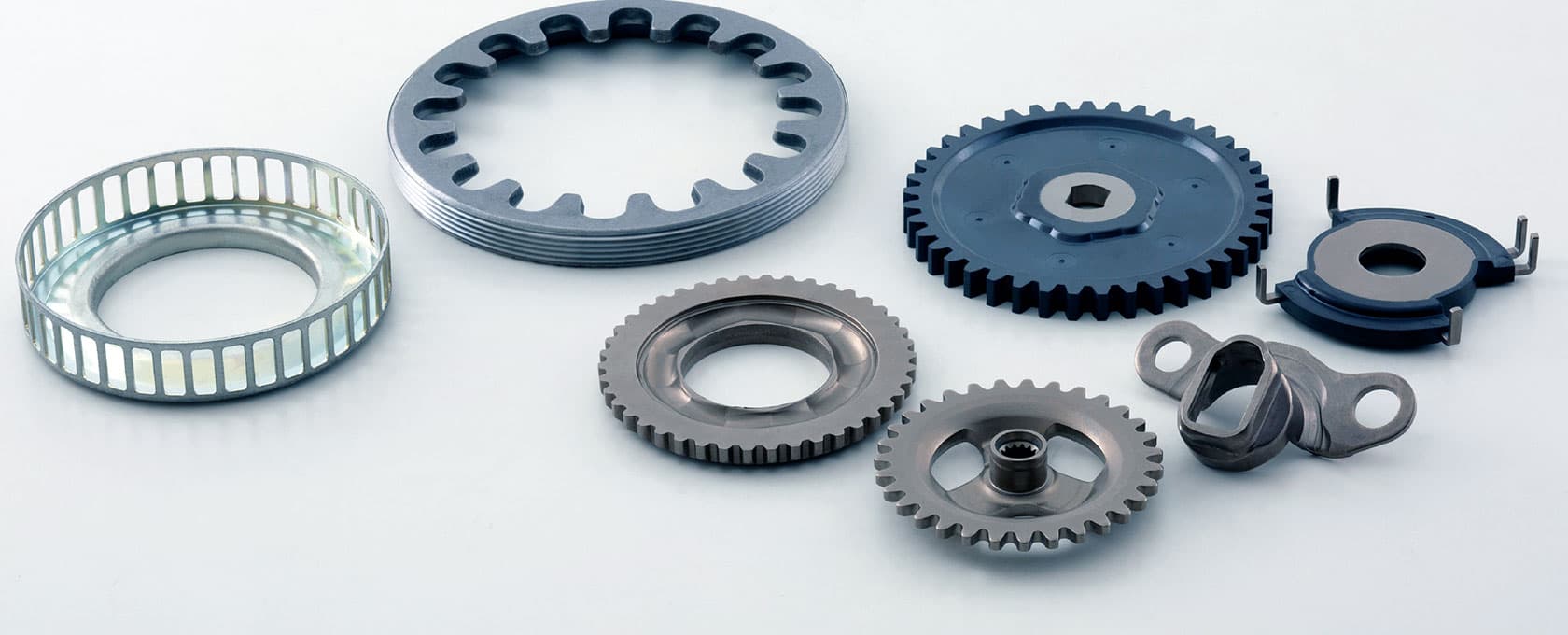
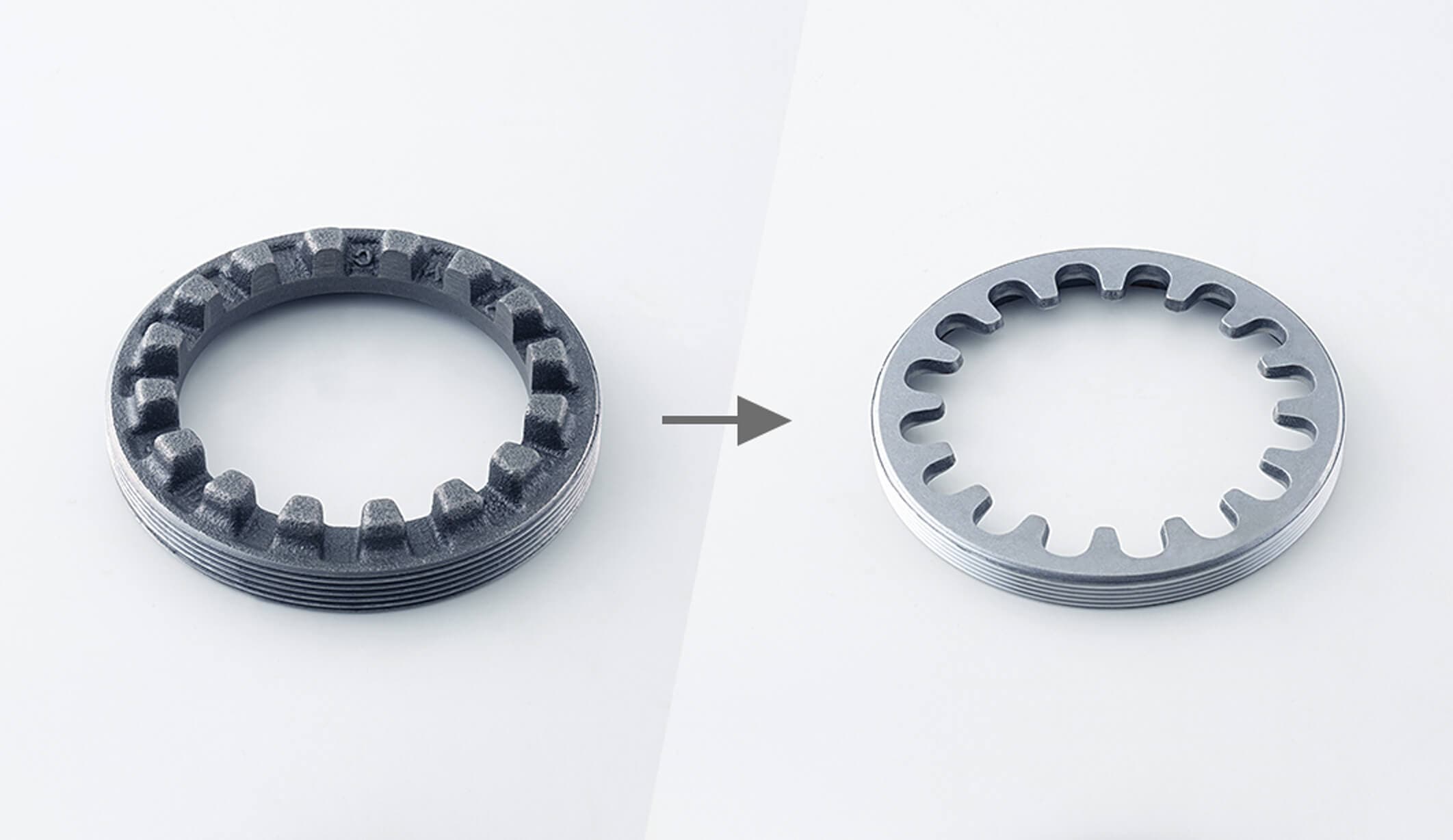
従来の「焼結品」から「プレス加工」への工法転換によるコストダウンを実現
事例概要
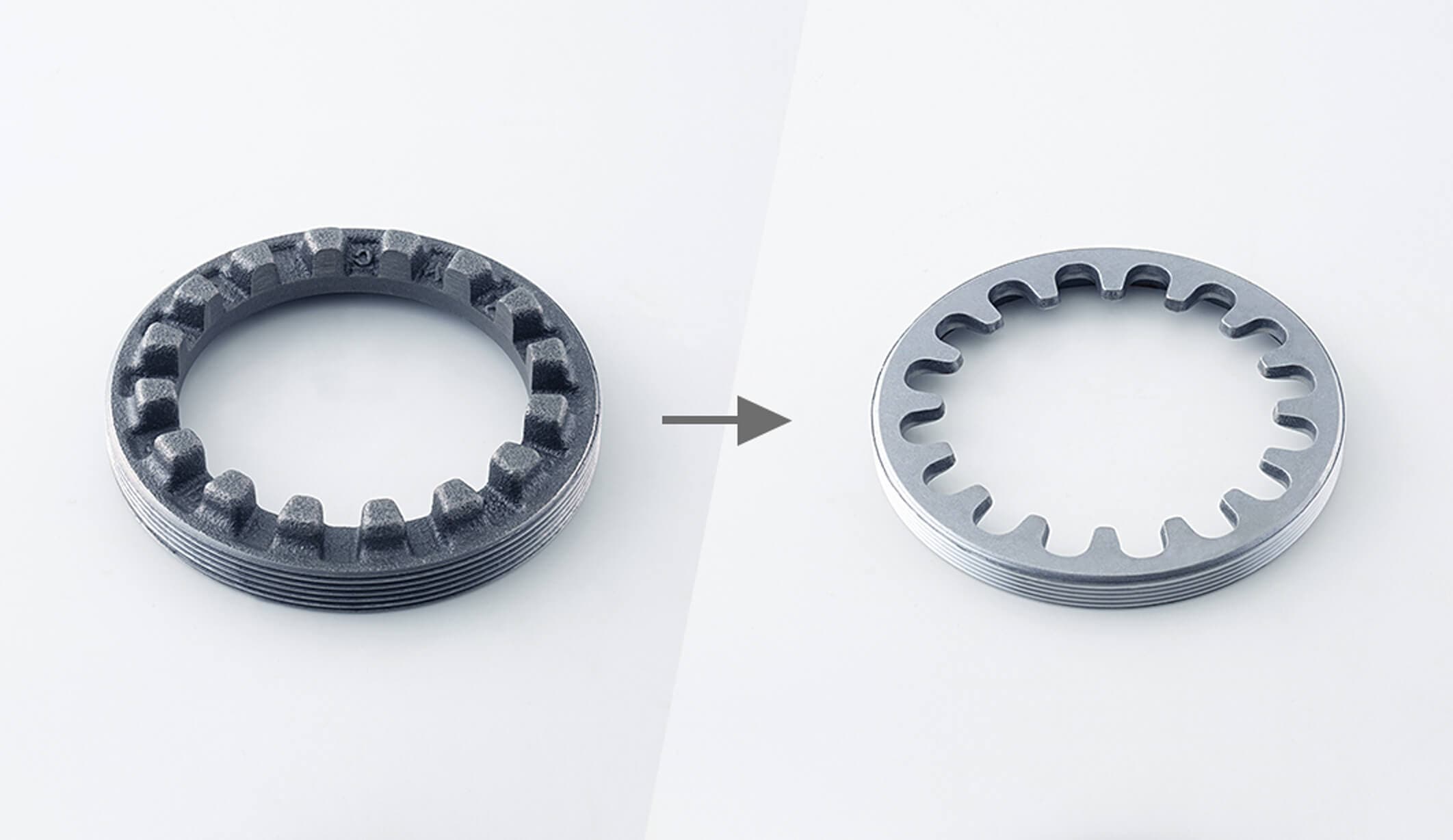
焼結、ねじ切り切削の工法から、プレス、ねじ切りの工法への転換に成功しました。機能を満足できるVE提案として、他社従来部品よりも約15%の価格低減と軽量化を実現しております。
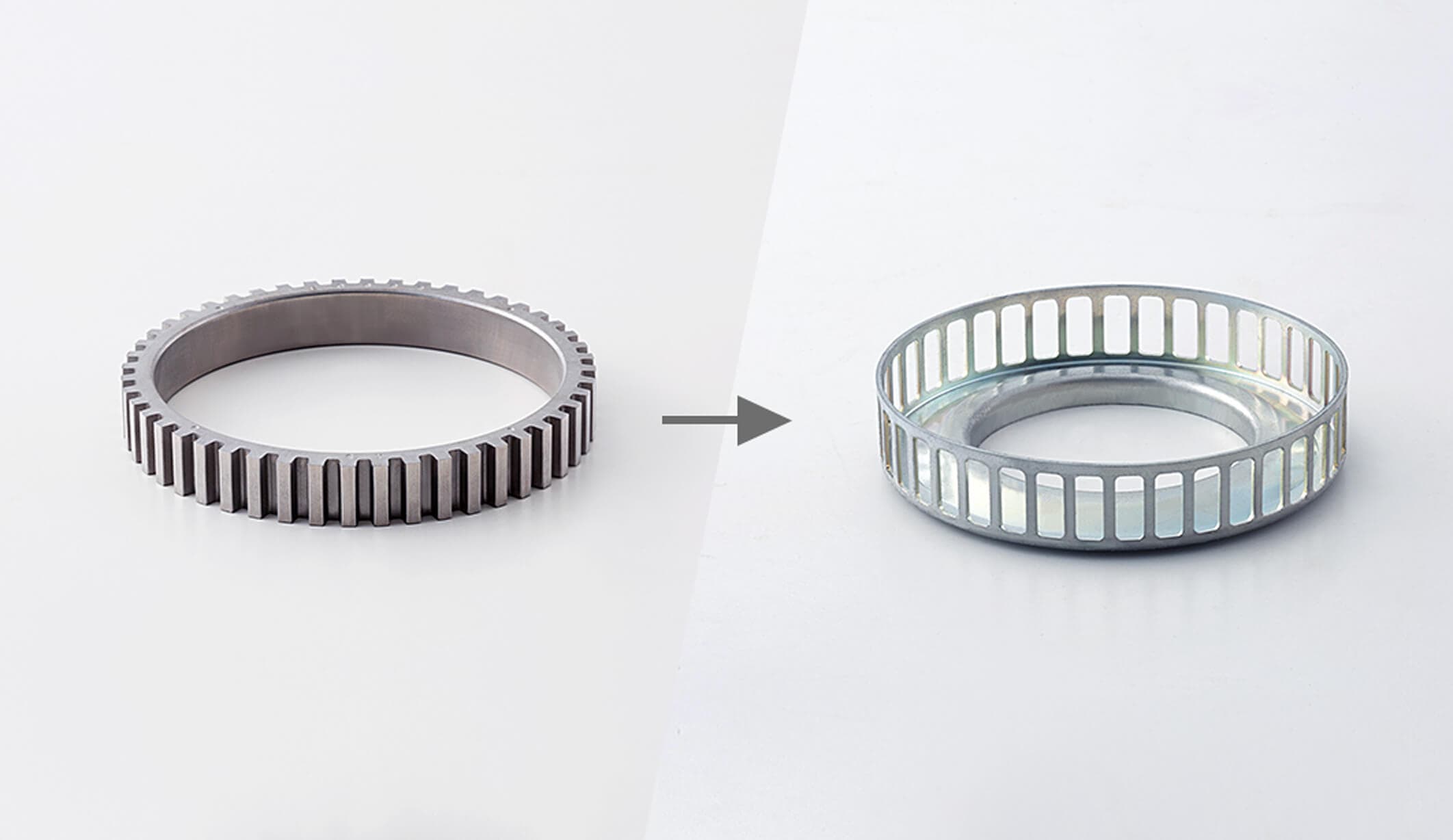
従来の「焼結プレス加工」からの工法転換によりコストダウンを実現
事例概要
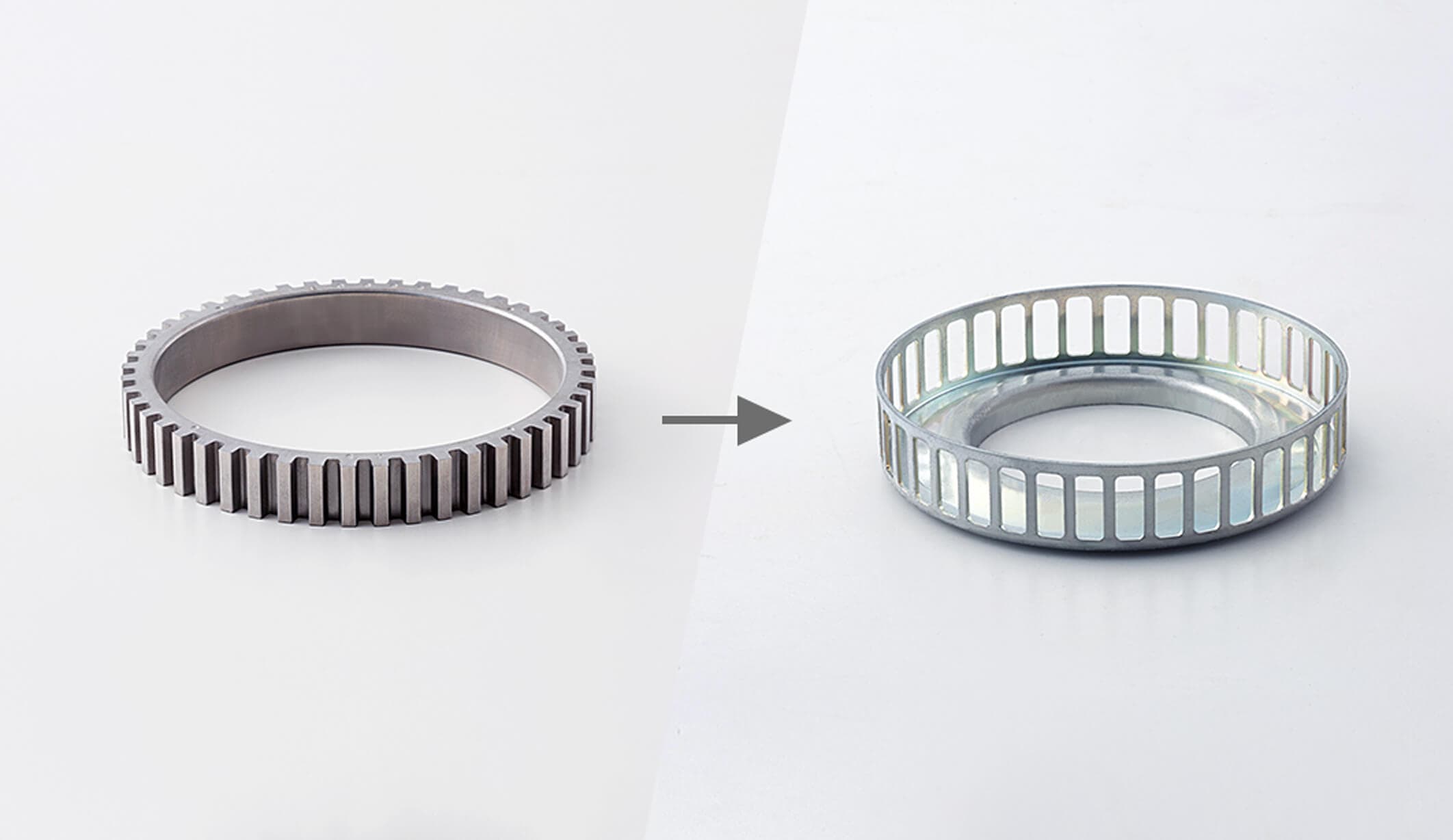
デファレンシャルのスピードセンサー部品の焼結品のセーシング部位を窓抜きのプレス形状によるVE提案になります。さらに窓の精度や内径の圧入精度についても要求機能を満足させ、30%のコスト削減を実現しております。
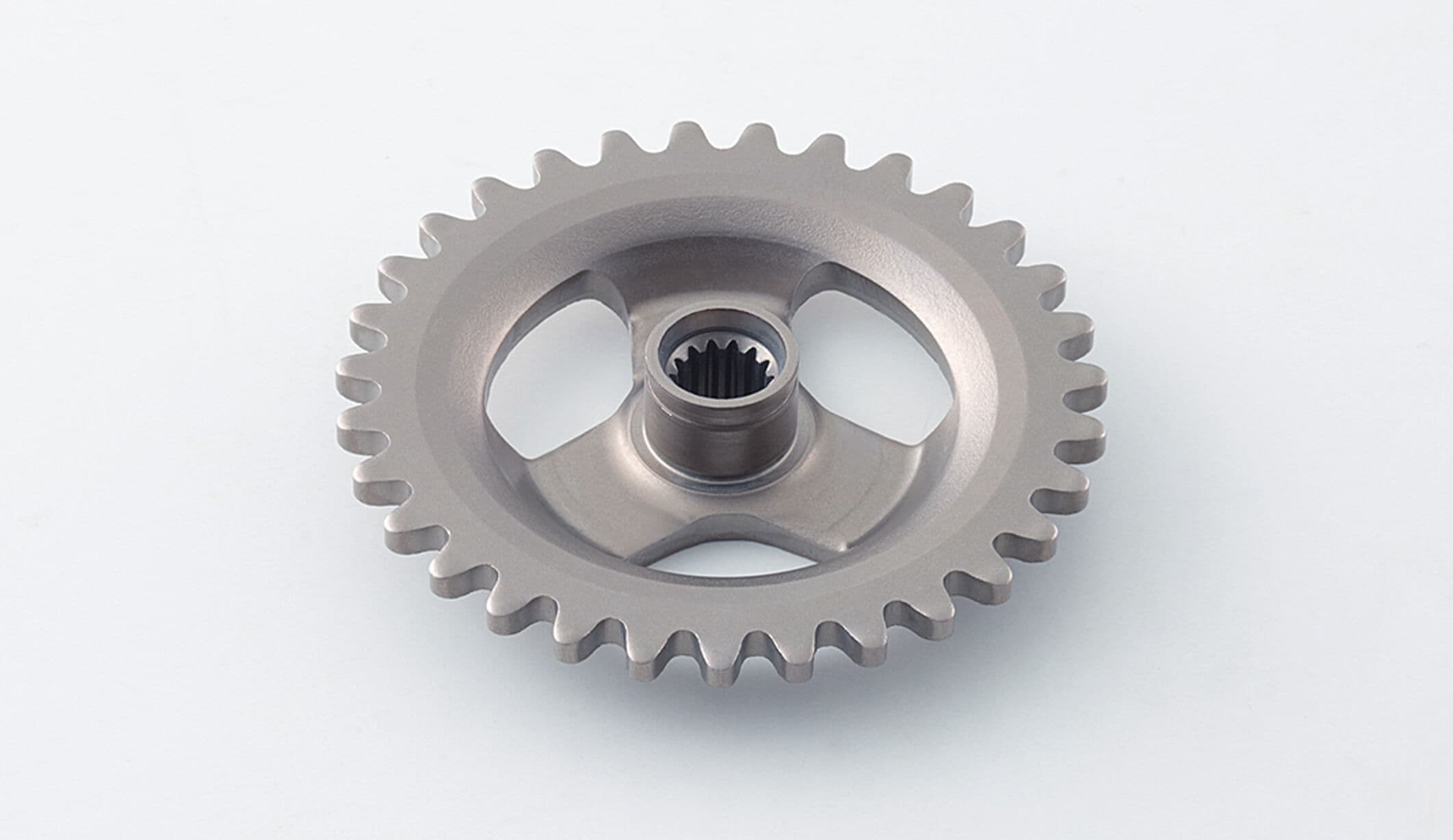
技術的に困難とされてきた内径部のプレス化に成功
事例概要
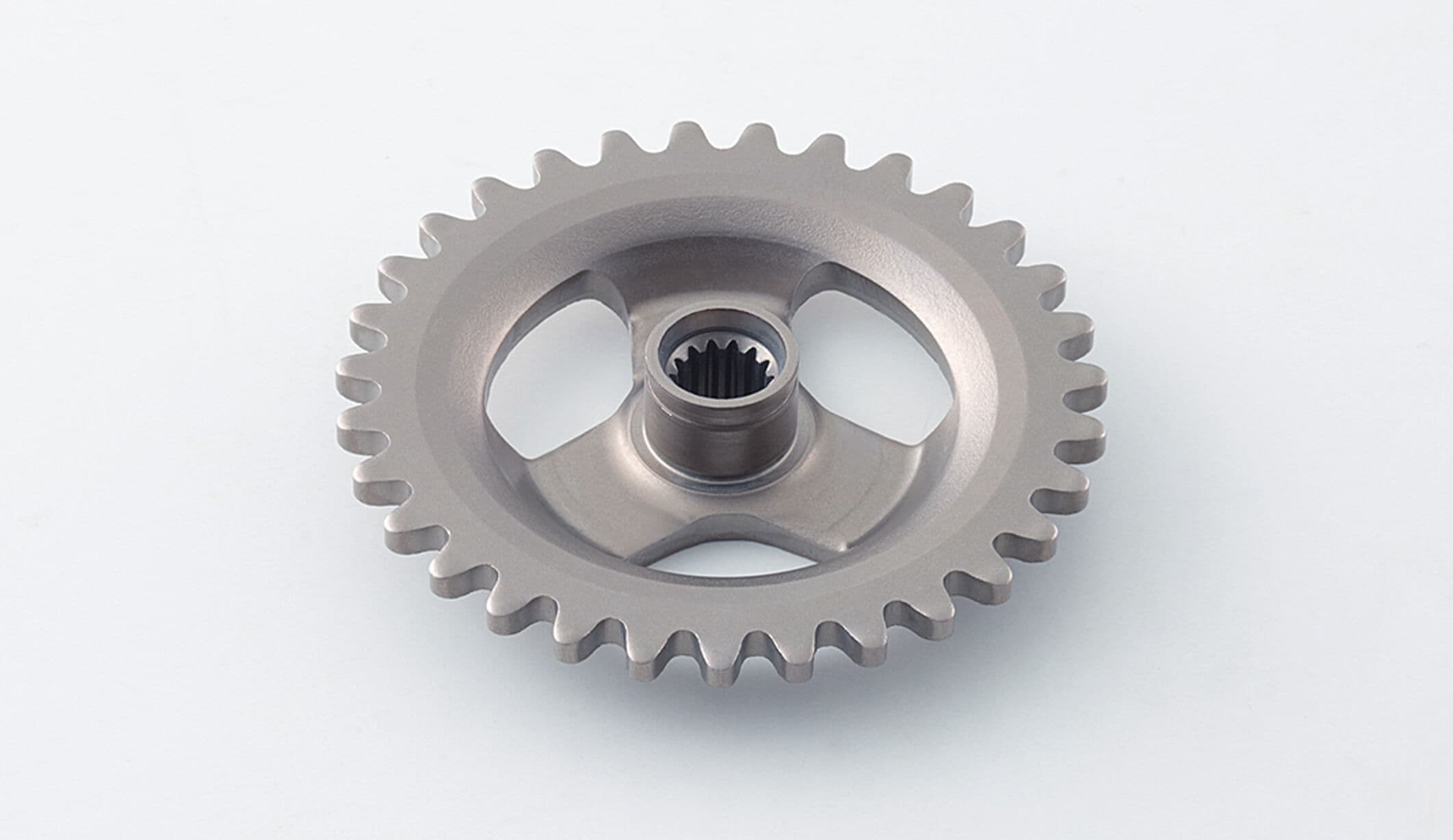
従来、内径部をブローチ加工で製造していたものを、プレス加工に転換するVE提案になります。25%のコスト削減と生産能力の向上を実現し、技術的に困難とされてきた内径部のプレス化に成功しております。
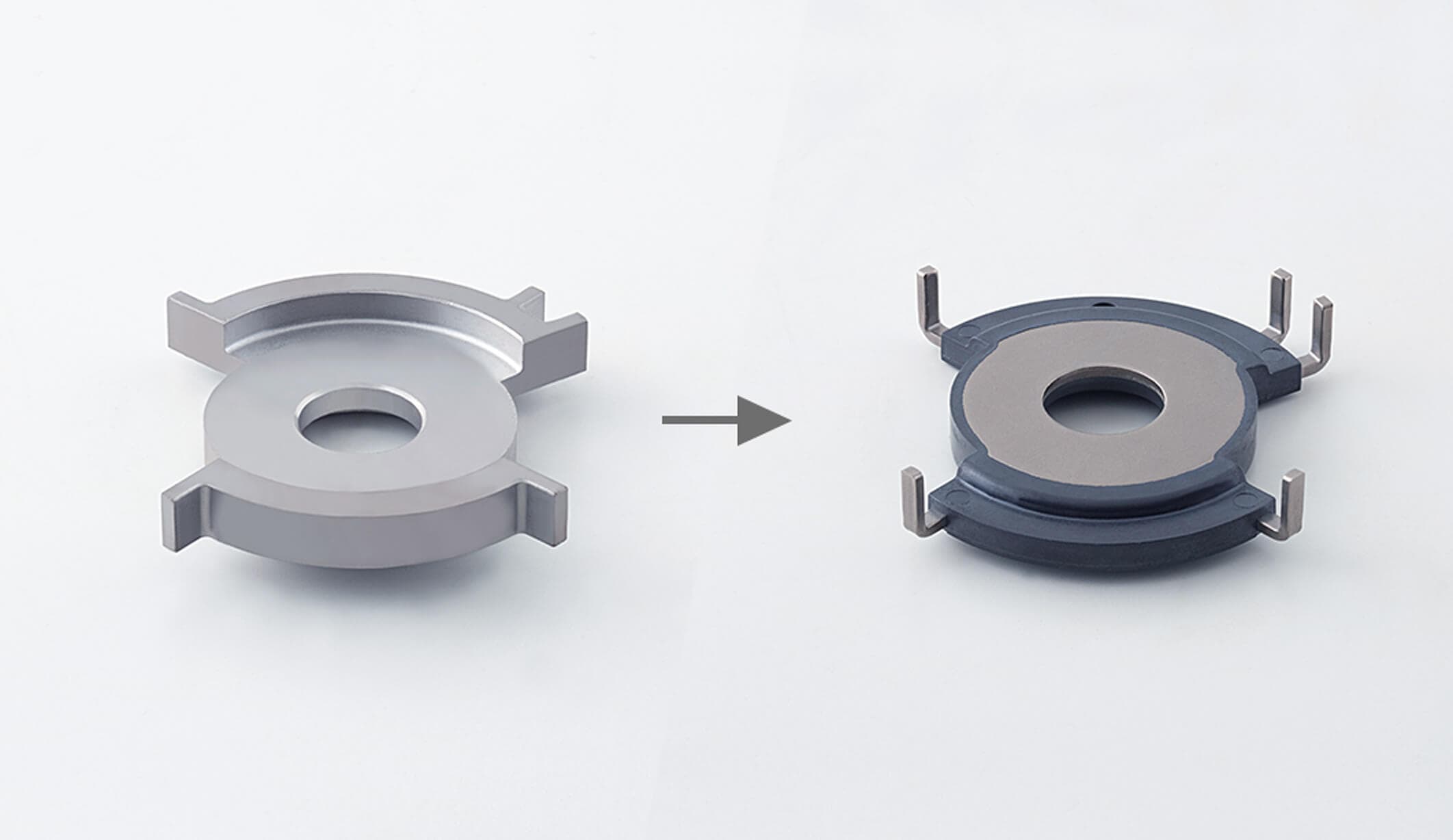
樹脂材とインサート成形することにより大幅な軽量化
事例概要
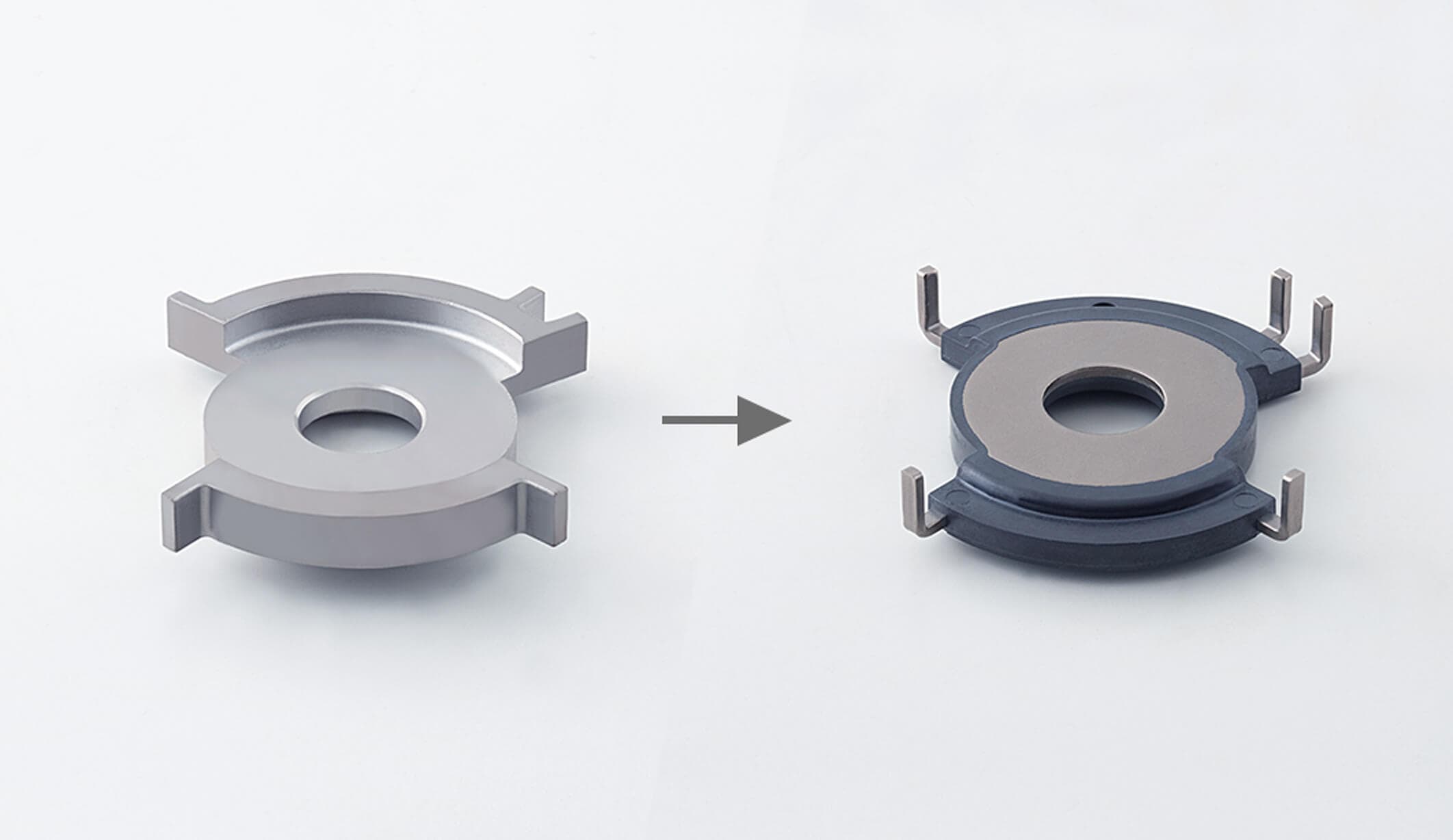
成形品従来焼結工法の厚みを確保するため、必要部を鉄、厚み部を樹脂として強度と軽量化に成功しております。金属と樹脂の長所を生かしたハイブリッド成形品になります。
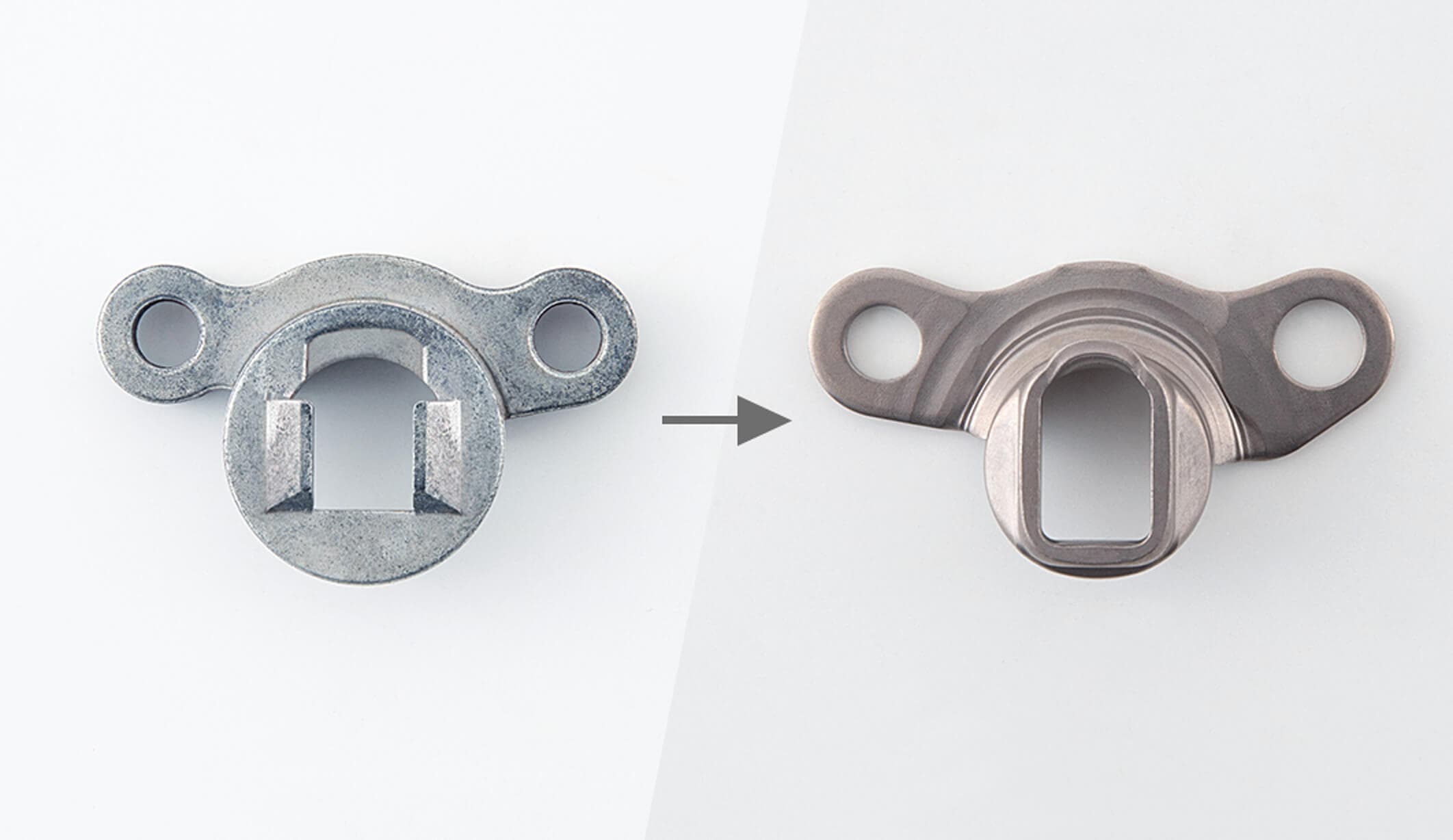
オールプレス加工の工法転換によるコストダウン
事例概要
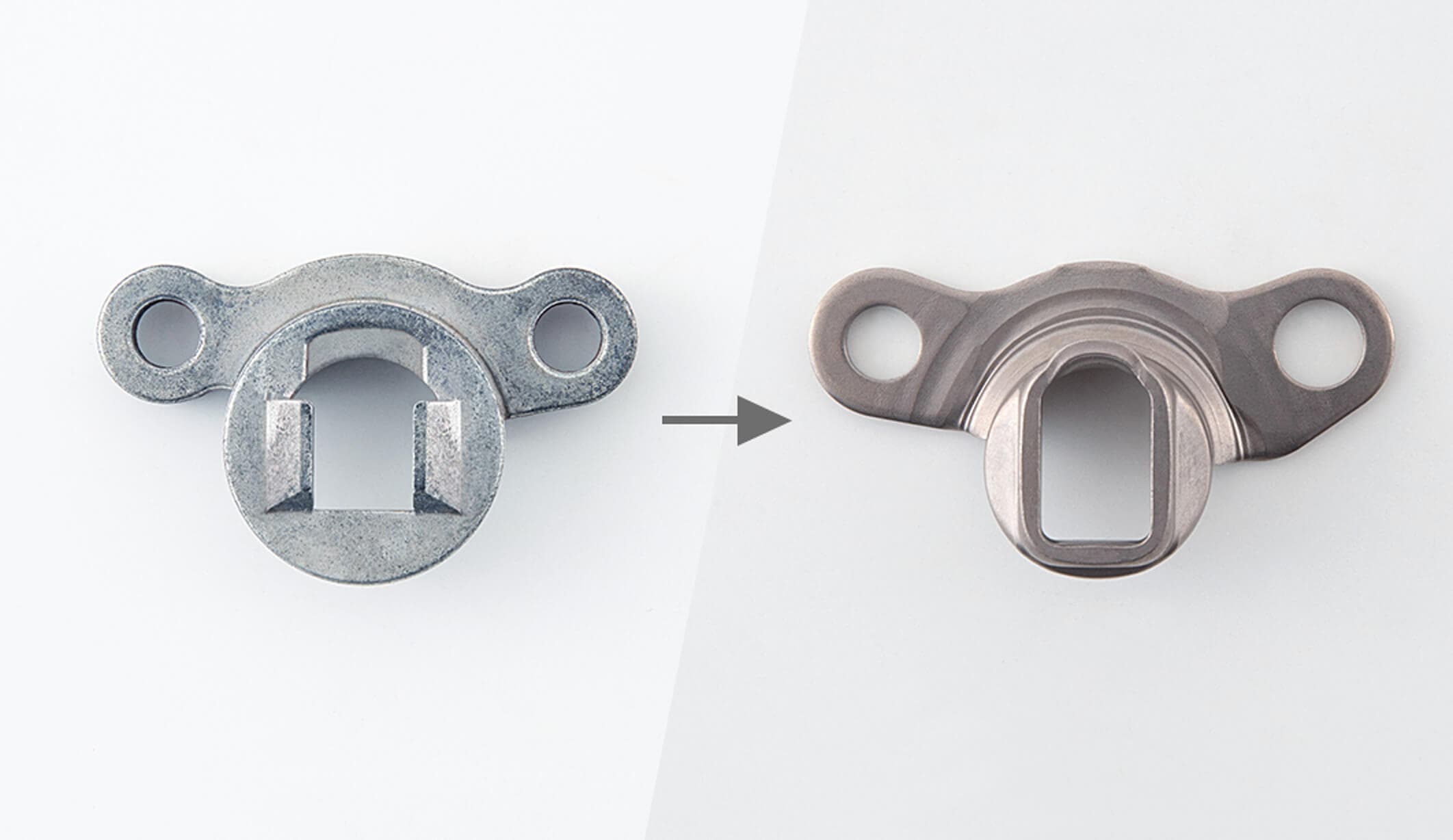
従来の「焼結および機械加工」から「オールプレス加工」への工法転換によりコストダウンを実現しております。表面の硬度は浸炭窒化にて確保しております。
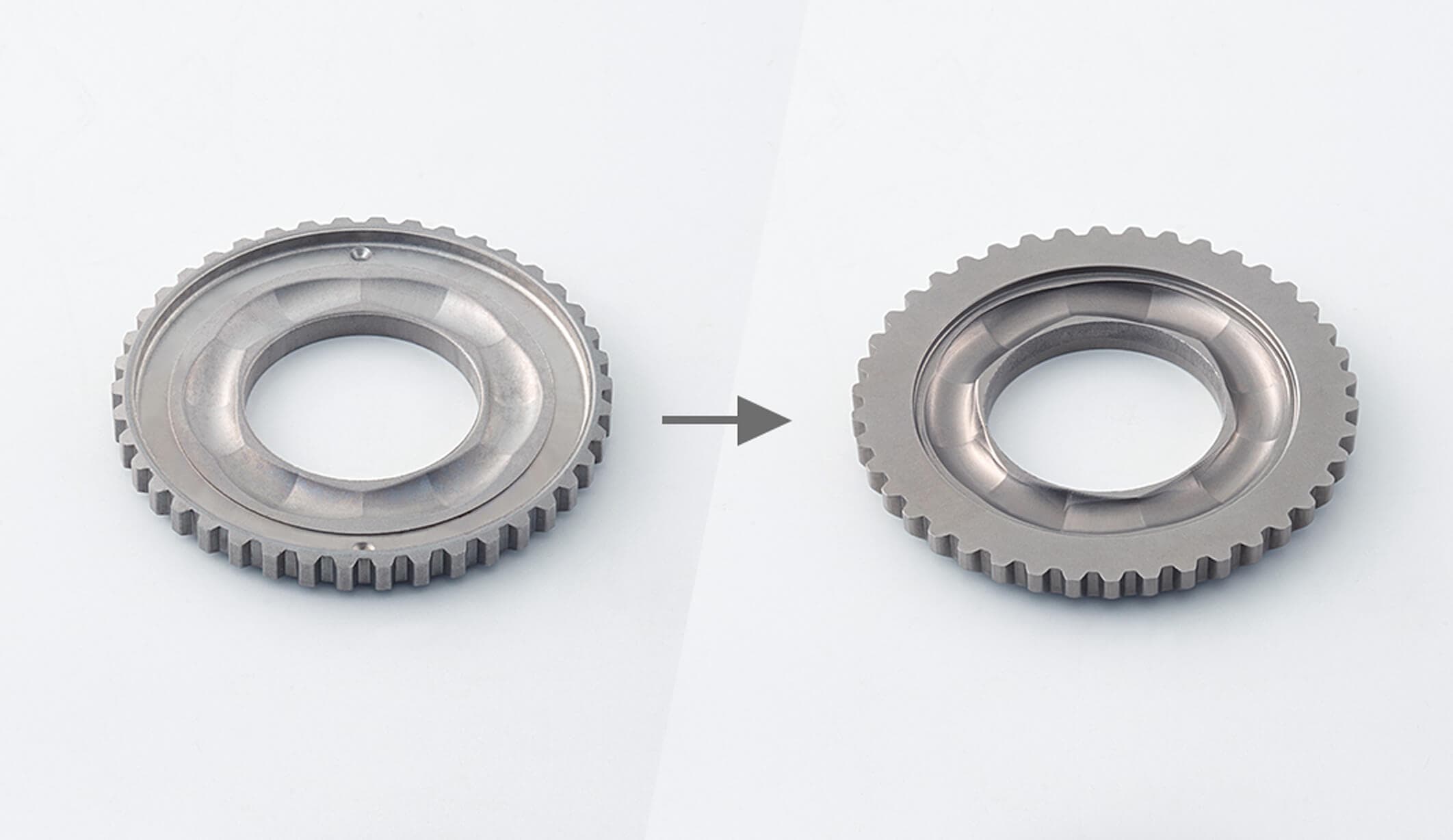
従来の「焼結および面切削加工」から「プレスおよび面切削」への工法転換
事例概要
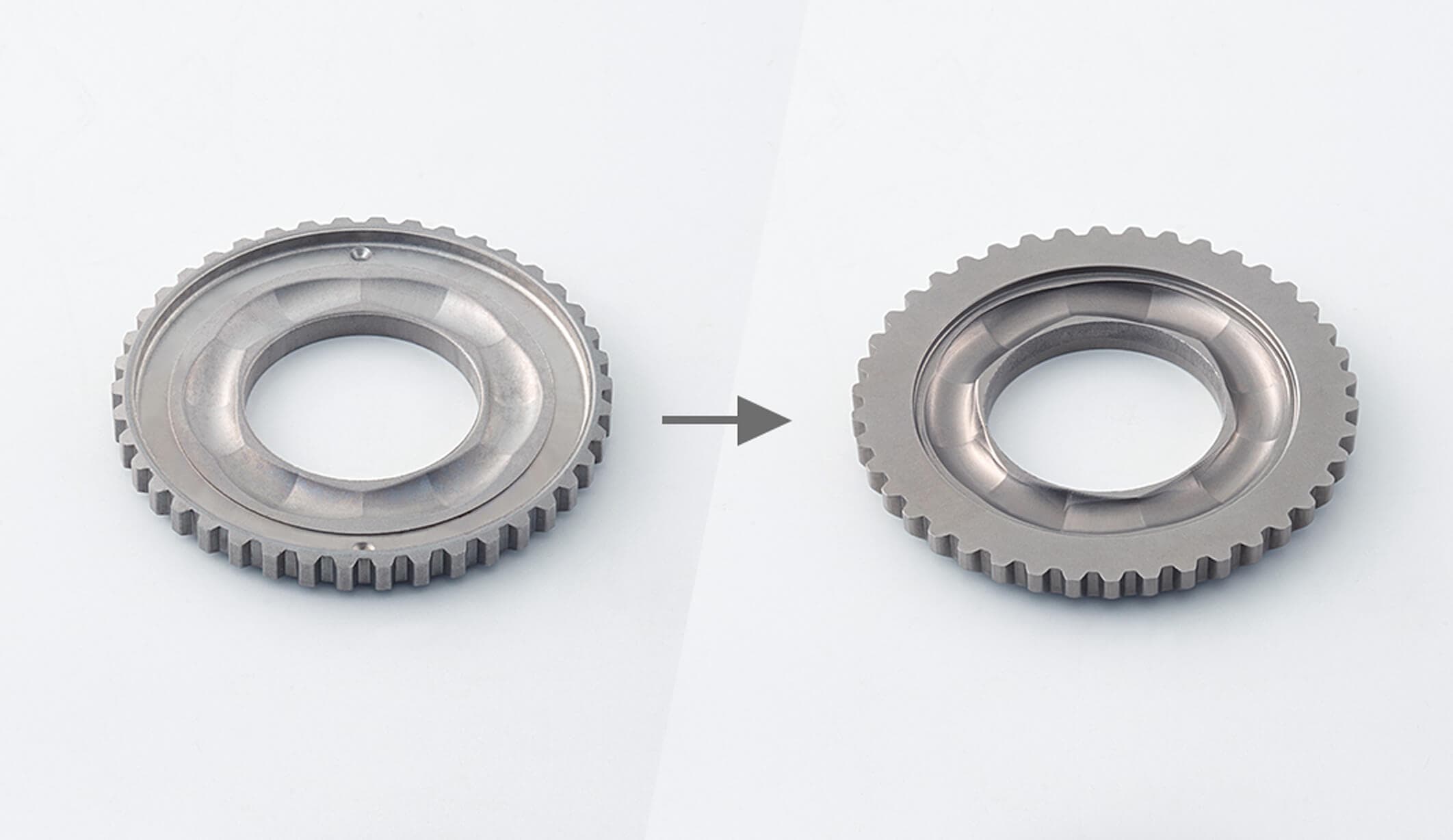
従来、焼結加工していたものを「プレスおよび切削」へ工程変換しコストダウンを実現しております。表面の硬度は浸炭窒化にて確保しております。
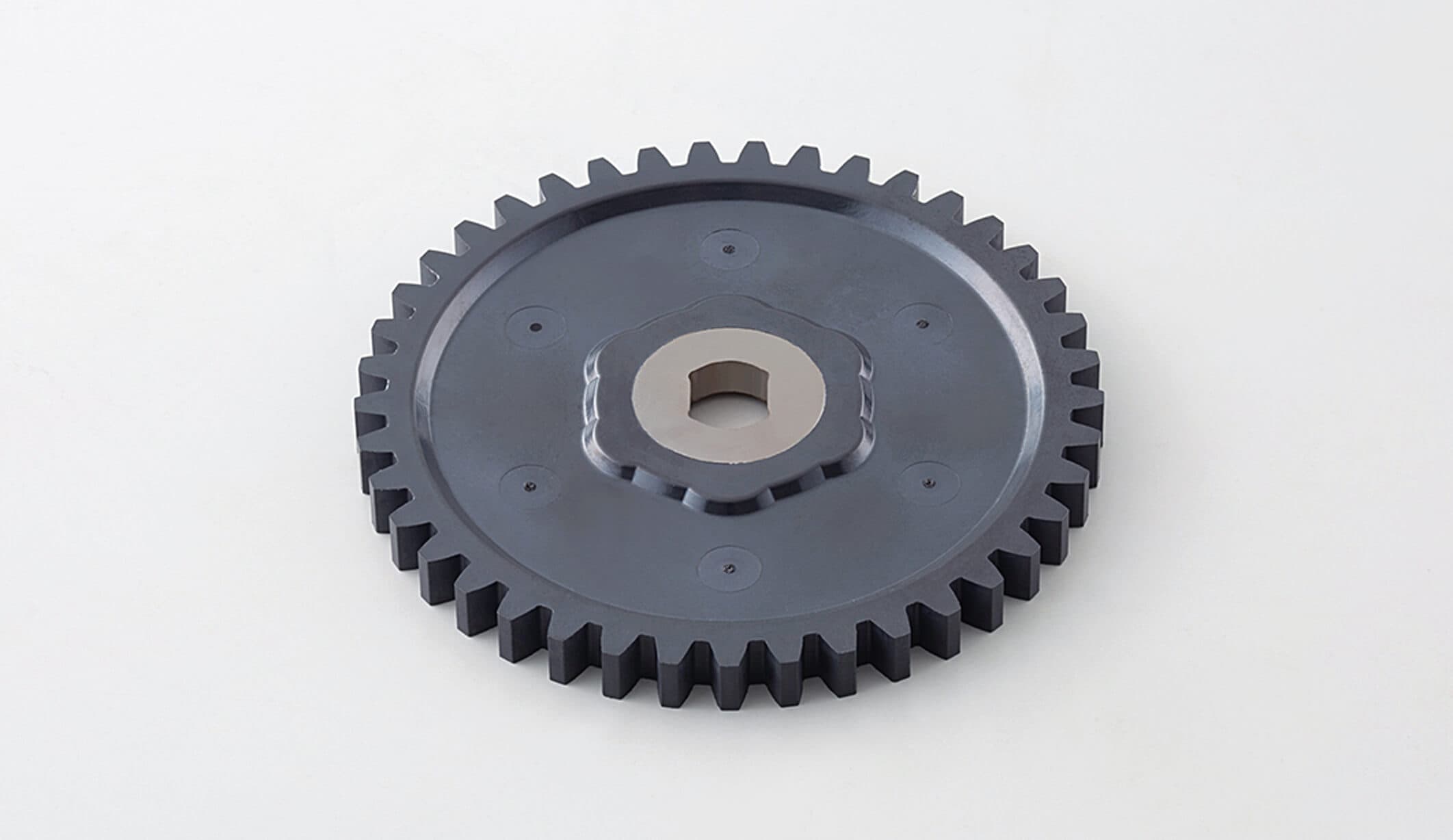
歯車を樹脂化しコストダウンと軽量化に成功
事例概要
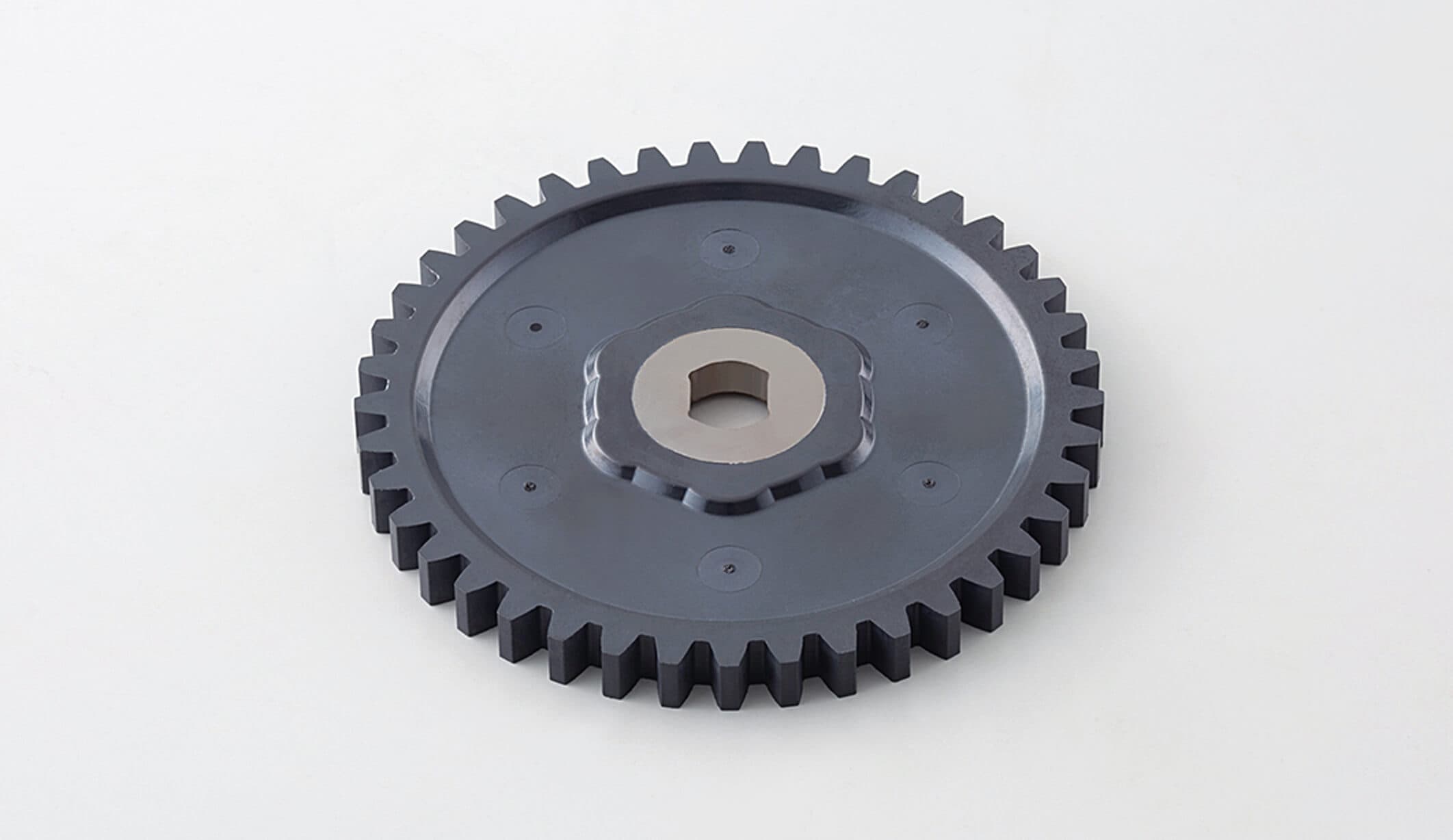
「鍛造および歯切削工法」から、「締結部をプレス、歯部を樹脂化」しインサート成形に成功し、強度アップと軽量化を実現しております。