Pressing spline shapes for O.D. gears and I.D. gear.
Products
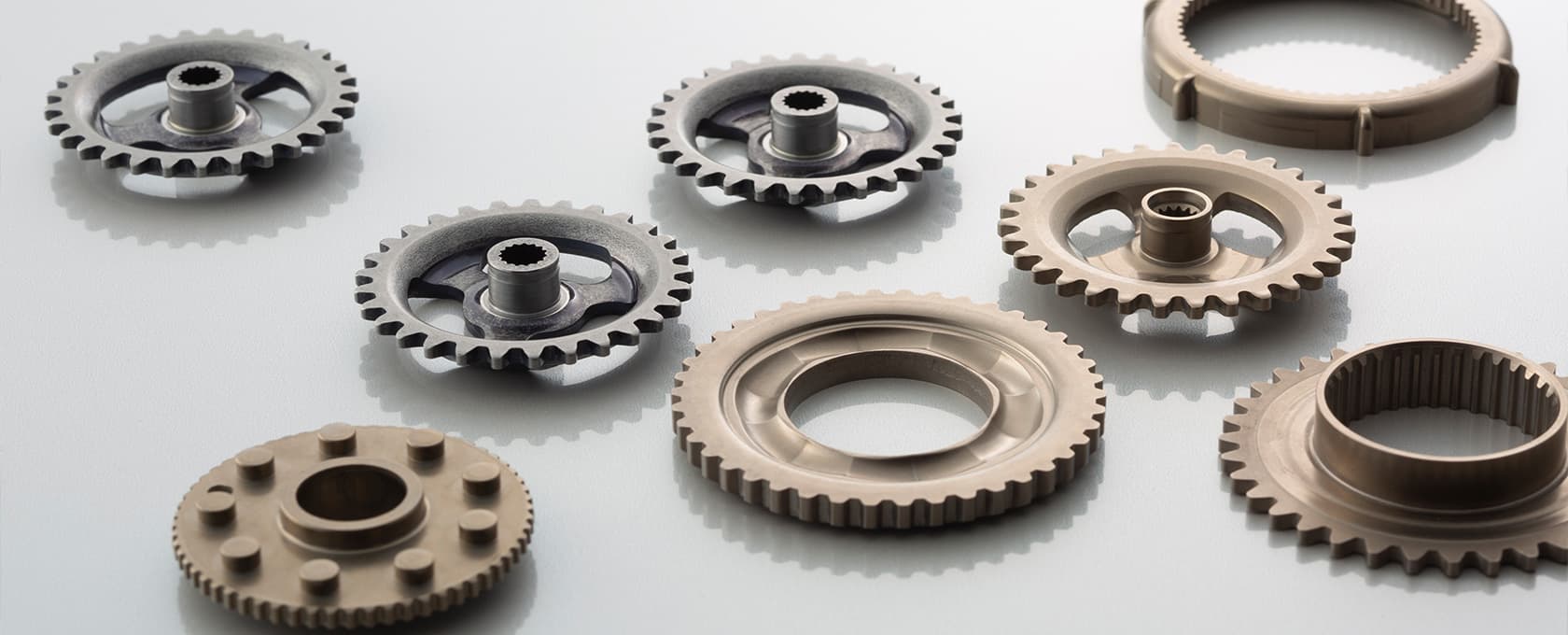
Inner Diameter Thickening Processin
-
Sprocket for Oil pumps
Usage:Oil pumps for transmisison -
Gear Sun
Usage:Electric actuatorsUsing a transfer press, we machine a tooth profile with a shear face of 70%, a protruding profile at 9 locations, and a protruding profile on both sides of the inner diameter.
Precision Shearing
-
Sprocket for Oil pumps
Usage:Oil pumps for transmisisonPressing spline shapes for O.D. gears and I.D. gear.
-
Sprocket Drive
Usage:Electric bicycles drive partsUsing only pressing, the center 8 mm is raised, machined into a spline shape on its inner diameter, and its dimension is secured, from a plate thickness of 2.9 mm.
-
Sprocket
Usage:Oil pumps for transmissionsPrecision press enabled us to change from the conventional sintering method to press-worked inner diameter splines.
-
Gear Ring
Usage:Electric actuatorsThe transfer press is used to form the tooth shape of the inside diameter and the outer circumference.
-
Gear Sun
Usage:Electric actuatorsUsing a transfer press, we machine a tooth profile with a shear face of 70%, a protruding profile at 9 locations, and a protruding profile on both sides of the inner diameter.
-
Sprocket
Usage:Engine camshaftsWe have succeeded in reducing costs and weight by proposing "press + carbonitriding" instead of the conventional "sintered + induction hardened products." We work on sprockets of various shapes.
-
Crank Angle Sensor
Usage:Engine crankshaftsHigh-precision machining of outer sensing area.
-
Gear Sprocket
Usage:Electric variable valve timing systemSintered products are processed by all-press. Gears in the inner diameter section are shaved to ensure 80% shear surface.
Precision Plate Forging
-
Cam Pilot
Usage:4WD unitsThe conventional sintering method has been changed to pressing. Furthermore, carburizing and nitriding achieved cost reduction and increased strength.
Extrusion Processing
-
Forged Gear (Extrusion method)
Usage:Reduction unit gearsPressing is used to form the outer tooth tips by applying pressure from above and below.
Precision Molding Processing
-
Motor Rotor Magnet End Plate
Usage:Hybrid motorsHigh-precision forming of SUS material with rolling anisotropy is realized.In particular, the stepped forming of the oil channel portion for motor oil cooling reduces warping distortion.
-
Adapter
Usage:Air conditioning unitsAluminum material is formed into complex shapes. In addition, processing with minimal burr.
Insert Molding
-
Gear Pulsar
Usage:Engine camshaftsWhile maintaining the features of products conventionally formed by the sintering process, the combination of steel and resin not only reduces weight, but also ensures strength.
-
Insert Gear
Usage:ActuatorsThe outer gears, which require strength, are pressed from steel to ensure accuracy.We proposed resin insert molding for the areas where strength is not required to make them light.
-
Gear
Usage:Water pumpsForging + tooth cutting method" was changed to steel press for fastening part and tooth part was changed to insert molding product. Multi-materialization has made this product stronger and lighter.